Micro Abrasive Waterjet Advantages & Disadvantages
The Finecut waterjet cutting technology uses a high-pressure jet stream of water to cut virtually any material. Fine grains of abrasive are added to the jet to increase cutting power. The waterjet process is flexible in many aspects, it can cut any material and by adjusting a couple of parameters you can reach different levels of tolerances, surface finish or economy. Finecut waterjet machines are manufactured with the highest quality parts to ensure accuracy, durability, consistency in surface and edge quality and they are easy to operate and control. Below you will find further information about why our technology is useful.
What Are The Benefits of abrasive waterjet cutting?
- Superior surface finish and edge quality
- Ultra-High Precision
- 3D Cutting
- Non-Thermal cutting
- Cuts Virtually Any Material
- …or thicknesses
- Capable of complex geometries
- Easy and low cost set up
- Less material waste and higher cost saving
- Eco-Friendly Cutting Technology
- Speak With A Waterjet Specialist
- What can a waterjet not cut?
Superior surface finish and edge quality
The waterjet process does not bring any mechanical damage to the cut surface. The top edges of the cut may become slightly rounded from stray particles leaving the jet. This can be avoided by using a sacrificial material on top.
Surfaces produced will be free from adverse mechanical and thermal effects and in general requires no subsequent machining to remove damaged material from the product. The cut surface is smooth and has no burrs, the harder the material is, the better Ra value you will get. Normally, surface roughness values below 1.6 µm (Ra) can be accomplished, and for hard material roughness values below 0.8 µm (Ra) are often obtainable.
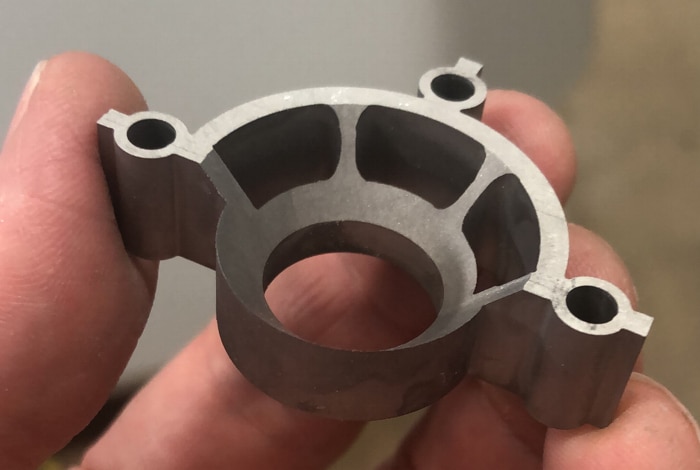
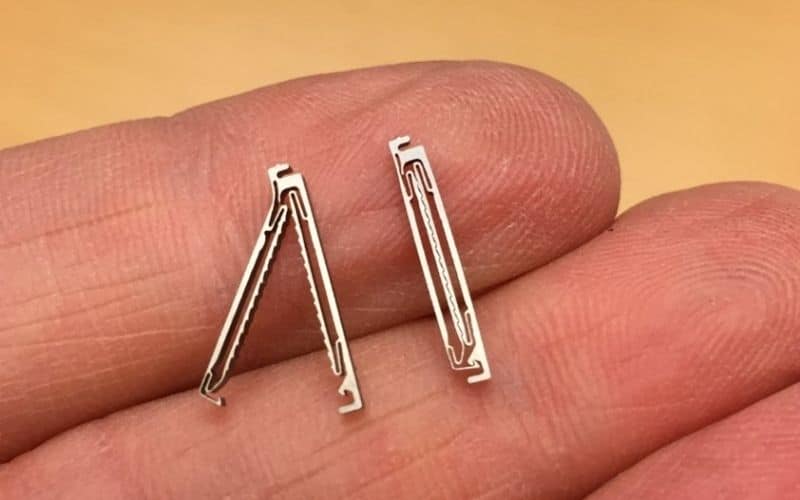
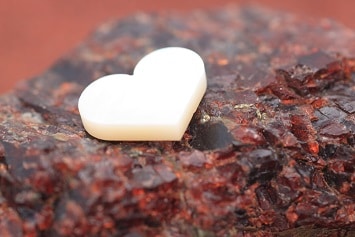
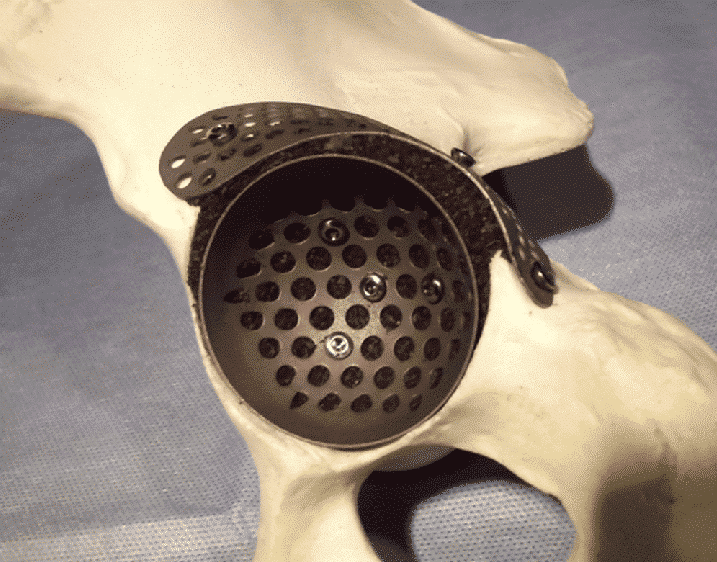
Ultra-High Precision
Finepart micro abrasive waterjet machines are 10 times more accurate than traditional waterjets.
The positional accuracy of a Finepart machine is ±2.5 micron and parts can be cut with ± 10 micron tolerance.
The repeatability of the machines is ± 2 micron. To achieve high precision parts, cutting speed and radius compensation is used actively to adjust dimensions to perfection.
Watch the video to see ultra-high precision as we cut Mother of Pearl on a fixture that allows a complete cut with no start/stop marks.
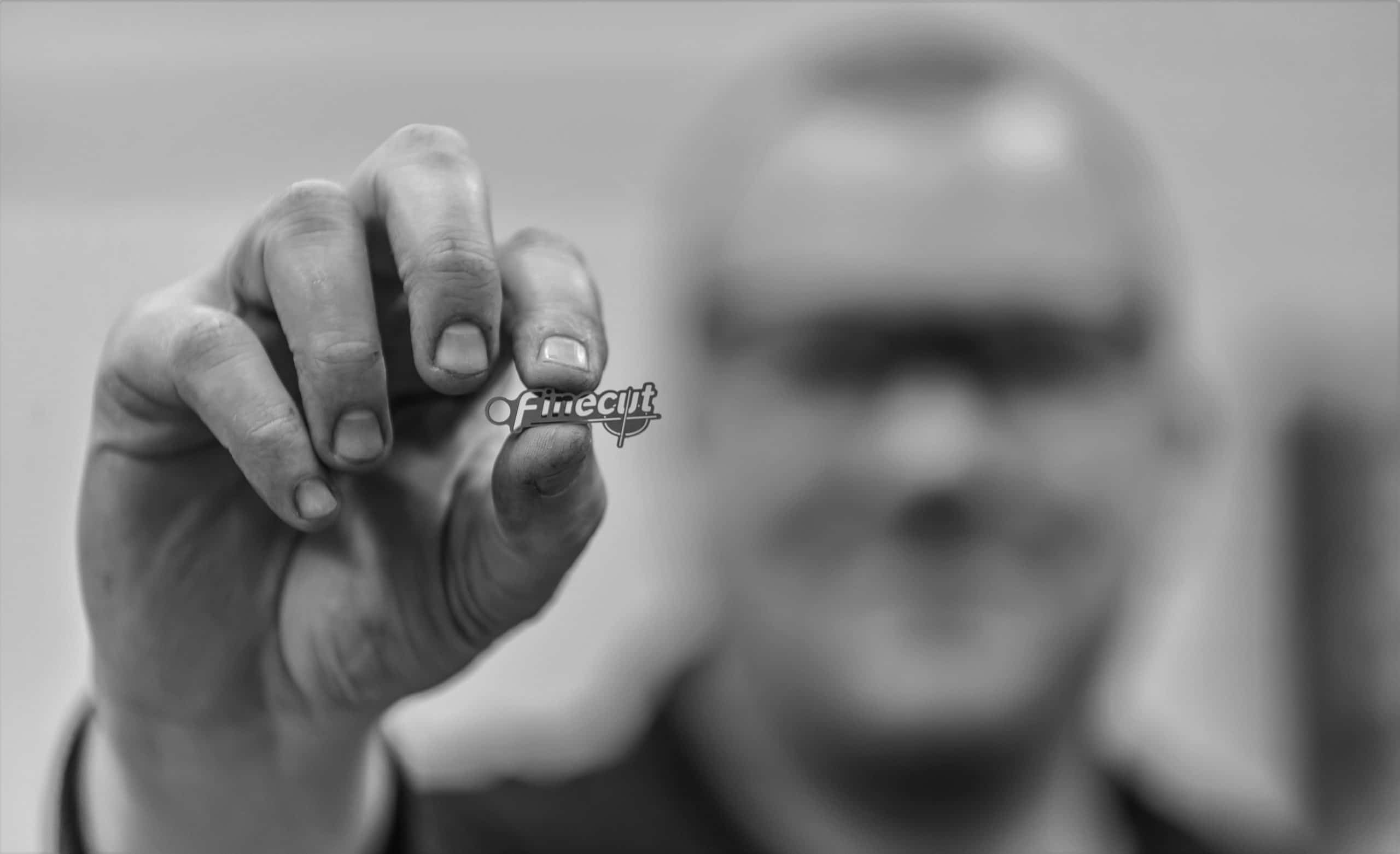
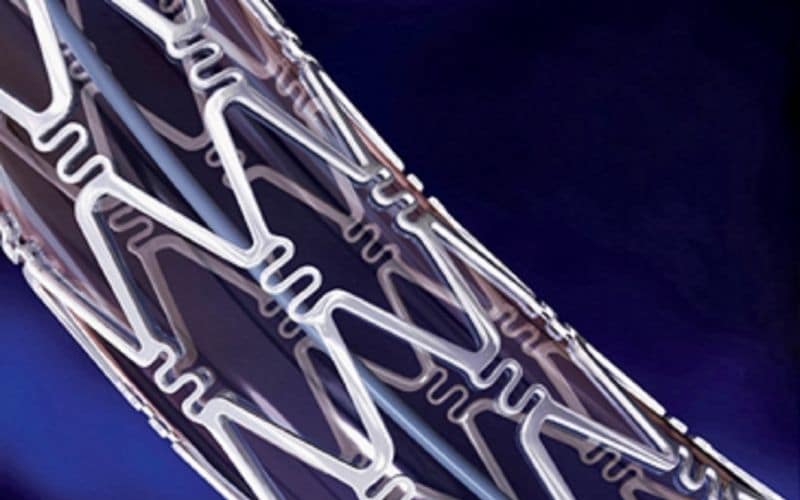
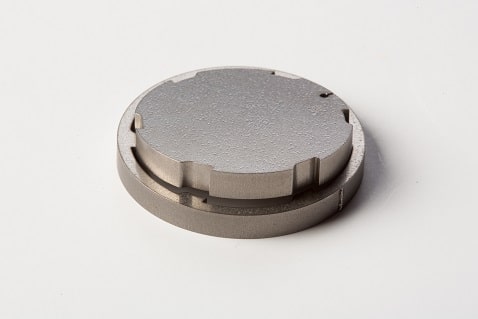
3D Cutting
By using multi axis configuration, very complex 3D geometries can be fabricated. Several waterjet machine manufacturers can offer 5-axis configurations for taper compensation and form error compensation. Those solutions are often limited in how many degrees the jet can tilt (below 10 degrees?).
Finecut 5 axis micro waterjet can tilt the cut cutting head +/- 15 degrees in all directions and this solution can be used both for taper compensation and to create angled cuts.
The Finecut 5 axis abrasive waterjet configuration is unique as it is capable of turning the workpiece 360 degrees and several sides can be accessed. The cutting head can tilt +/- 45 degrees in one direction and when it is combined with the turning table, very complex parts can be created.
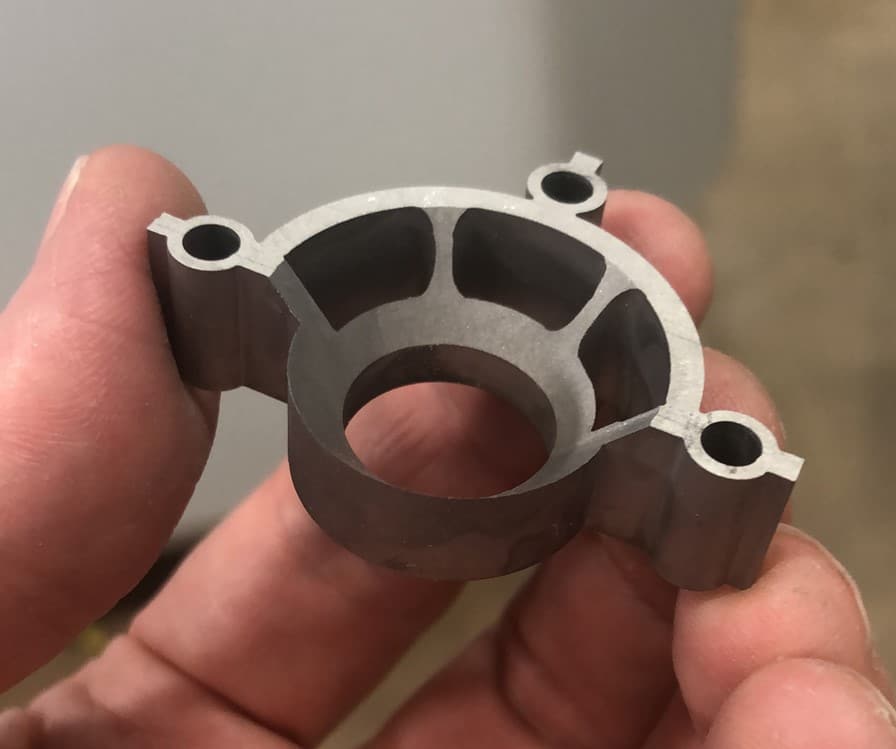
Non-Thermal cutting
The main advantage of the waterjet process is that it is a cold process, where no heat is generated during cutting. On a micro scale the erosion mechanisms momentarily create local heat upon contact but the continuous cooling by water will remove the heat and temperatures will cause no thermal effects on the cut surface. The fact that there is no heat affected zones or recast layers means that the material properties are maintained, and you can avoid micro cracks on the surface. A traditional cutting method like milling or turning will provide a heat affected zone that must be removed in a sub-sequencing process if you have an application where micro cracks are not allowed (applications sensitive for fatigue failure).
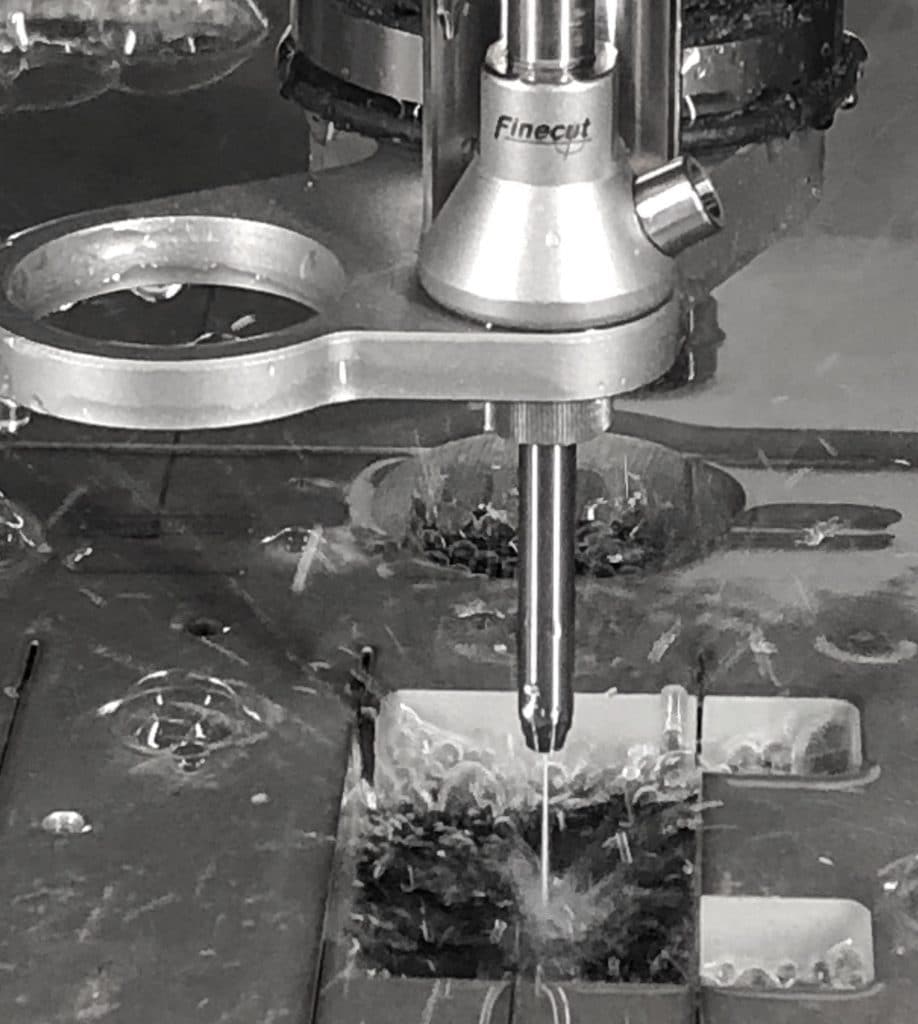
Cuts Virtually Any Material
The Finecut micro abrasive waterjet technology utilizes particle erosion for material removal. The fine thing with erosion is that it works for material removal in virtually all materials! When a fine stream of energized particles strikes the work surface, a range of erosion mechanisms are activated and cause material removal. The adaptive cutting process gives unique possibilities to cut combined materials. An example of a difficult combination of materials with disparate properties can be products that combine carbon fibre, titanium and epoxy.
The ability to cut various materials with the same tool setup as described above has the great advantage of user friendliness in the process. Basically, you may get started by running the same process for most cutting applications with only the cutting speed as variable parameter to obtain a cut profile and the cut quality required. Consequently, you can get started quickly producing parts.
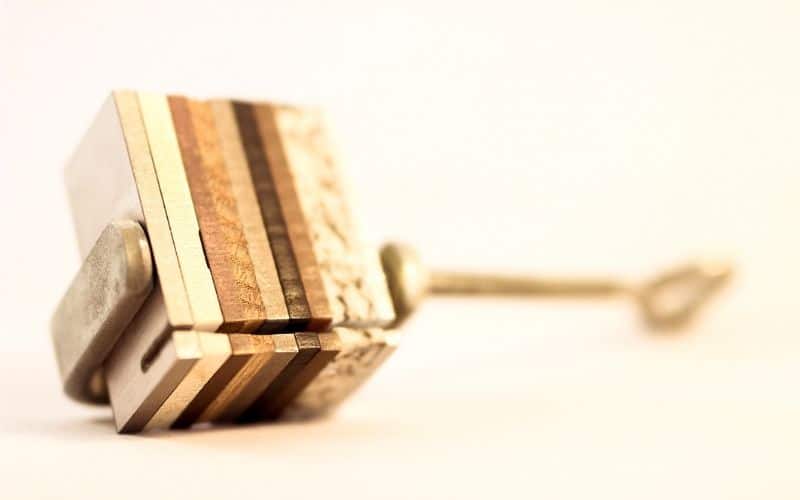
…or thicknesses
The micro abrasive waterjet process can be used for cutting material in different thicknesses. By adjusting the size of the nozzles in the cutting head, the process is capable of cutting thick materials like 300 mm stainless-steel, aluminium, or titanium. When using micro abrasive waterjet machines, the thickness is often below 30 mm as the size of the working table is limited and the ability to reach high tolerances is limited for thicker materials.
The small jet size and low cutting forces are of advantage when cutting really thin materials. We have cut 30-micron thick materials with good result, here it becomes important to find a good solution for material handling.
Thinner material can be stacked in several layers, however, gaps between layers should be avoided by clamping. Even small gaps between layers can cause delamination.
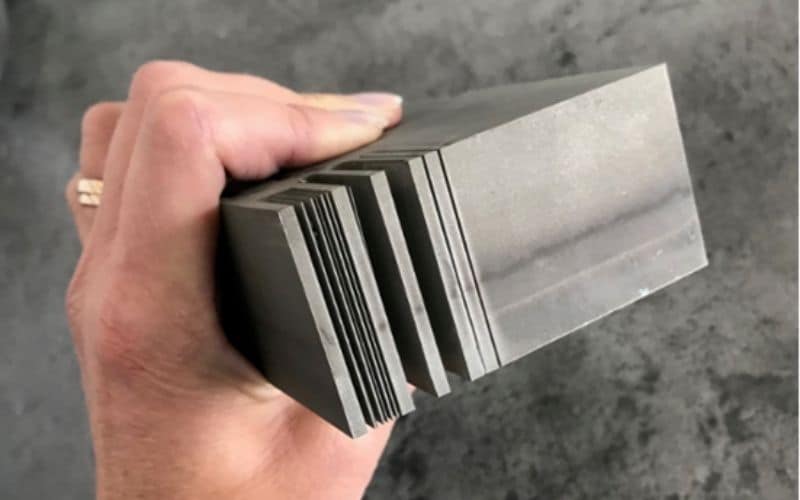
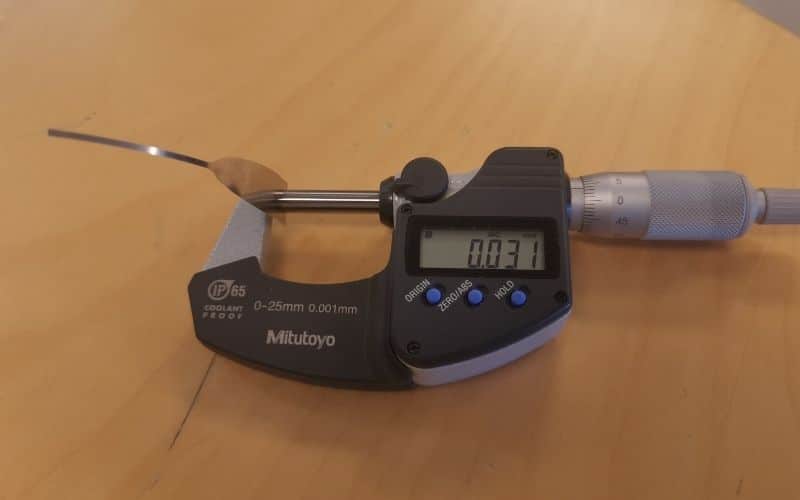
Capable of complex geometries
The jet can cut omnidirectionally which facilitates cutting highly complex geometries. Our technology cuts narrow slits down to 0.2 mm, narrow sections down to 0.1 mm, performs fine piercing for holes or a start for contours. Also, 3D features are cut with our 5-axis system.
Even if the jet velocity is high, the small flows of water give a very low force from the jet. Consequently, thin structures can also be cut without being affected by the jet forces.
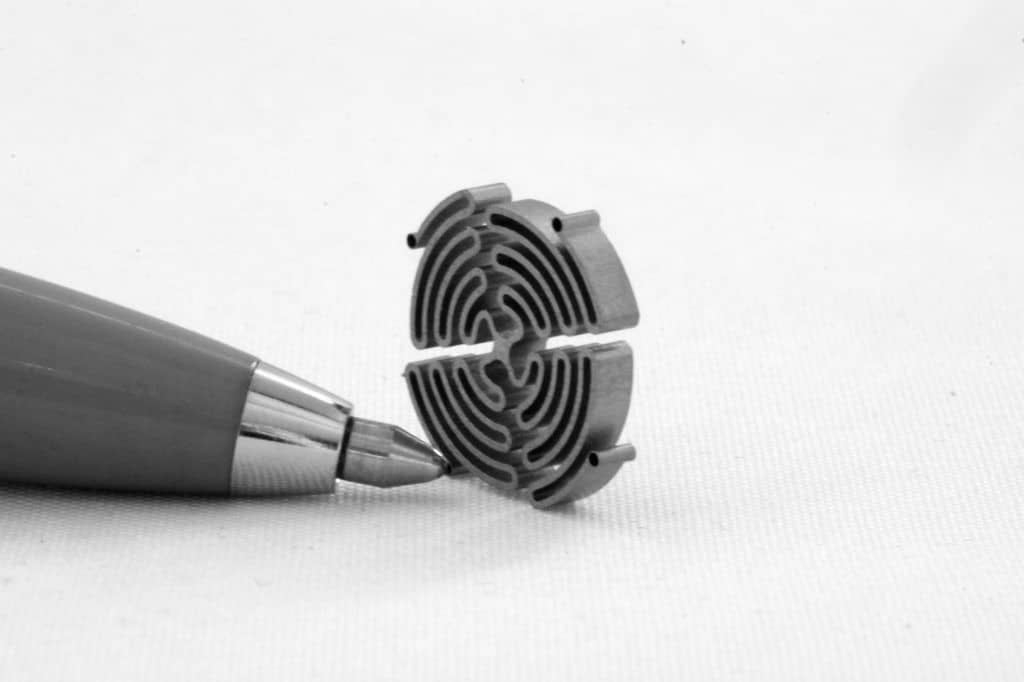
Easy and low cost set up
Using the CAD/CAM for waterjet programming allows the operator to create the parts in a few minutes. The cutting forces are low which means low requirements for clamping and fixturing. If there is no high demand for tolerances the material plate can just be put on the cutting table with a weight on top.
When using micro abrasive waterjet machinery for fine mechanic parts fixturing becomes more important. To reach really high tolerances the material must be kept still, even if the cutting forces are low. The jet causes an air flow from the drag force along the high-speed stream which is enough to move very thin material. Really thin materials can be attached to a carrier (eg. thin glass plate) and cutting is made through both materials. With the Finecut waterjet machines you can produce your own fixtures for cutting.
The same tool setup can be used for almost all materials.
Less material waste and higher cost saving
There is special CAD/CAM nesting software available for waterjet cutting. The software helps to lay out all of the parts in such a way that together they cover as much of the sheet or plate material as possible, thereby reducing the amount of waste. The program does this by testing various combinations of placement and orientation until it finds an optimal material utilization solution. Since the method offers a cold cut, without any heat affected zones near the cut, the parts can be placed very close to each other.
The absence of adverse effects on material properties, offered by cold cutting, also has the important advantage that finishing work can often be avoided. In thermal cutting operations, recast layers and heat affected material near the cut surface often need to be removed by a finishing operation. Avoiding subsequent finishing work by choosing abrasive waterjet cutting often means that the total cost of manufacturing a product can be lower than if the part were cut by a faster or cheaper thermal cutting method.
The Finecut waterjet machines offer narrow cut width of the jet, the diameter of the jet varies from 0.2 mm-0.5 mm depending on the size of the nozzles. A narrow cut saves material, which can be of great importance for expensive materials.

Eco-Friendly Cutting Technology
The abrasive waterjet operates by the same principles that have shaped the nature around us – particle erosion. This natural process works at low temperatures and does not produce hazardous gases while cutting. Cuts are clean and parts produced in a waterjet do in general not require chemical treatment or cleaning solvents before it is taken into use.
In the cutting process the used abrasive is collected in a catcher tank. If the material being cut is not poisonous the spent abrasive can often be used as landfill or even be recycled. Recycled garnet can be more effective in cutting compared to alluvial garnet as the edges are sharper.

Speak With A Waterjet Specialist
What can a waterjet not cut?
As described above, the micro abrasive waterjet cutting process is flexible and useful for many materials and applications. The list below describes some situations where the process is less suitable.
- Current technology limited to feature radii of ca 100 µm (i.e., the radius of the jet).
- Brittle materials with internal stress balance cannot be cut (e.g., hardened glass)
- Materials sensitive to water may not be suitable for cutting. Alternative liquids may be used in extreme cases.
- Materials of extreme hardness cannot be cut (e.g., diamond)
- Generates abrasive waste material that require to be disposal. In case of hazardous materials waste handling may be costly.