What Are Waterjet Cut Quality Classes?
The “waterjet cut quality classes” are a rating system for assessing the surface finish and cutting accuracy achieved by waterjet cutting. They refer to a scale used to define the quality of the cut edge. The scale ranges from the roughest cuts (Q1), called separating cuts, up to the most precise and taper-free cuts possible (Q5).
Cut quality classes are an important tool for aligning production quality with the final design application. Is the part used for demanding, high-precision applications like aerospace components or biomedical devices? If so, you’ll need to opt for a higher finished quality. On the other hand, if the part is just a prototype or if it will be finished by another processing method, opting for a lower quality class will mean faster and cheaper production.
The Traditional Waterjet Cut Quality Classification (Q1-Q5)
For the past three decades, the most widely referenced system for describing waterjet cut quality has used a ranking system with 5 levels. Cut quality classes range from Q1, for the fastest and roughest cuts, to Q5 for the smoothest and most precise cuts achievable with traditional abrasive waterjet cutting.
The origins of this system date back to Zeng and Kim 1992. While the system is more qualitative than quantitative, these classifications help operators determine the best settings for specific cutting needs.
Illustration of cut quality classification
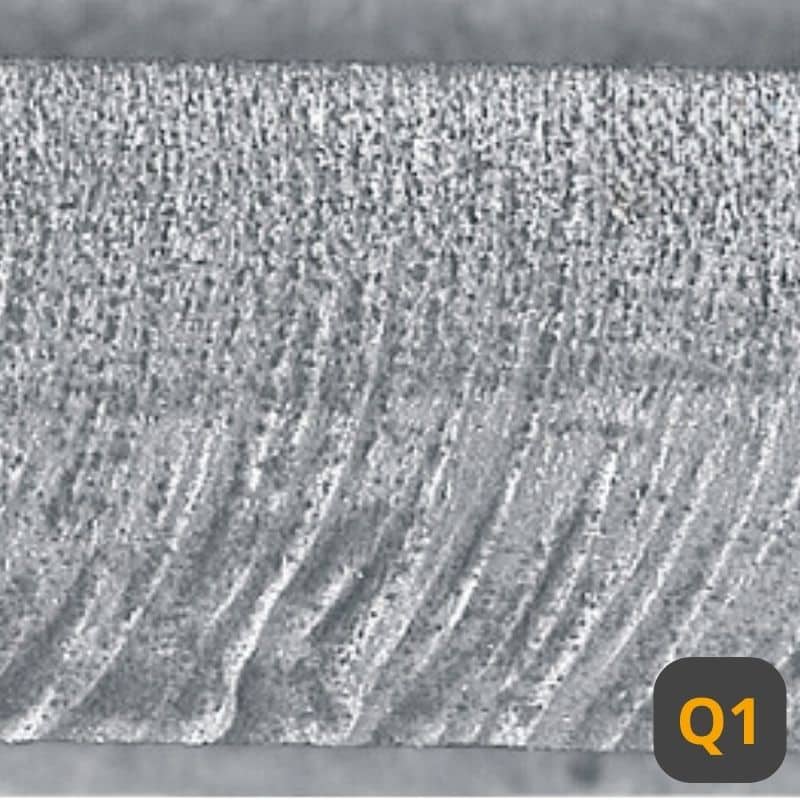
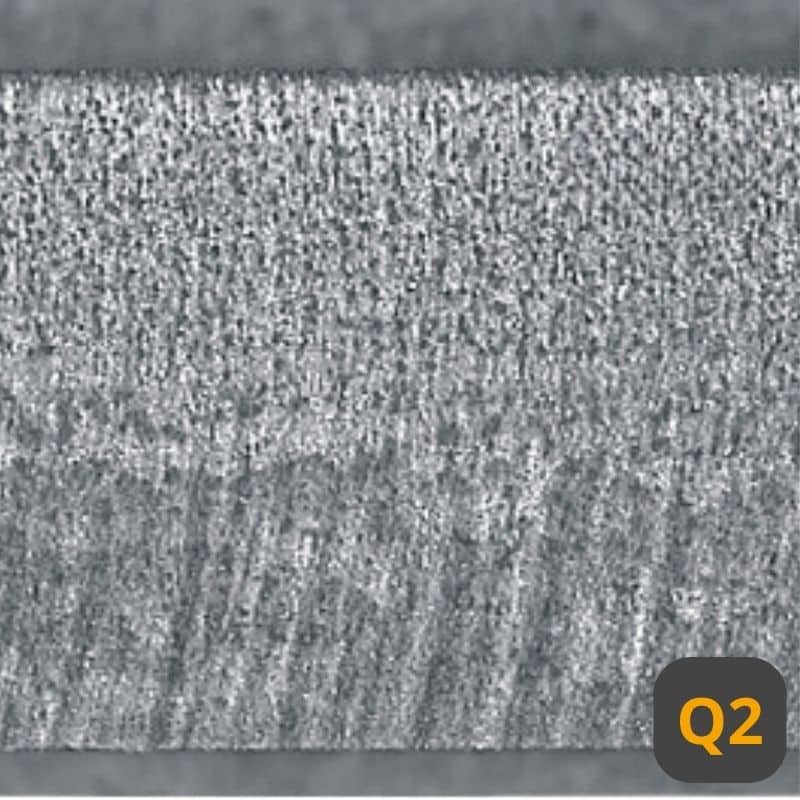
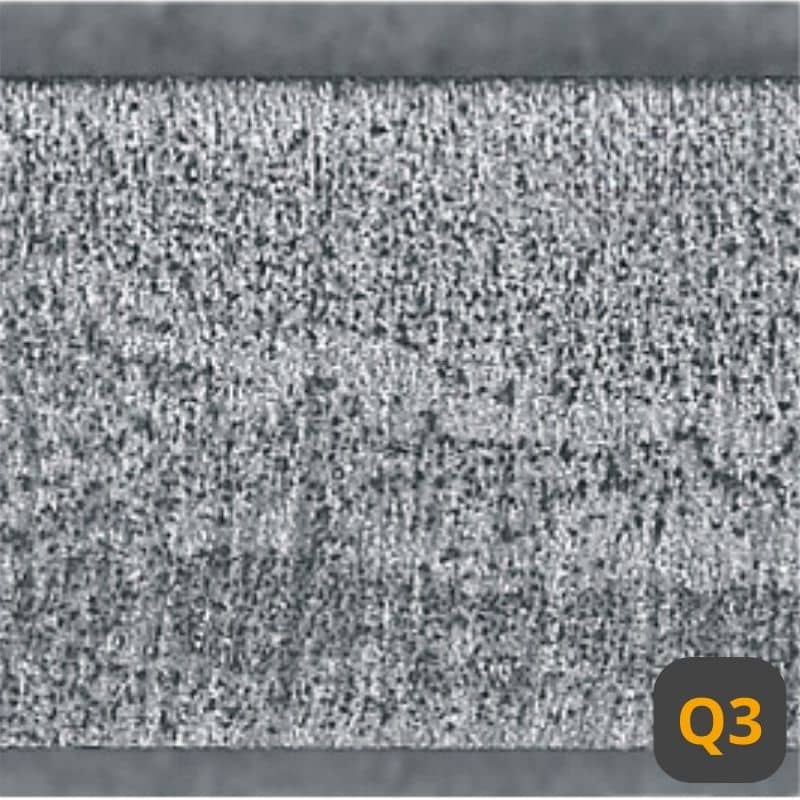
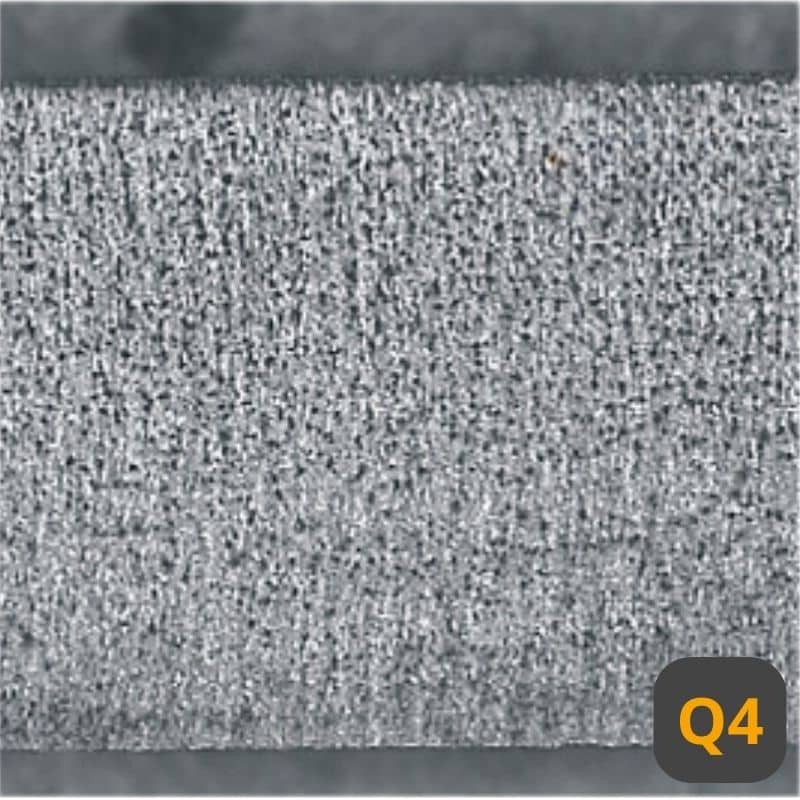
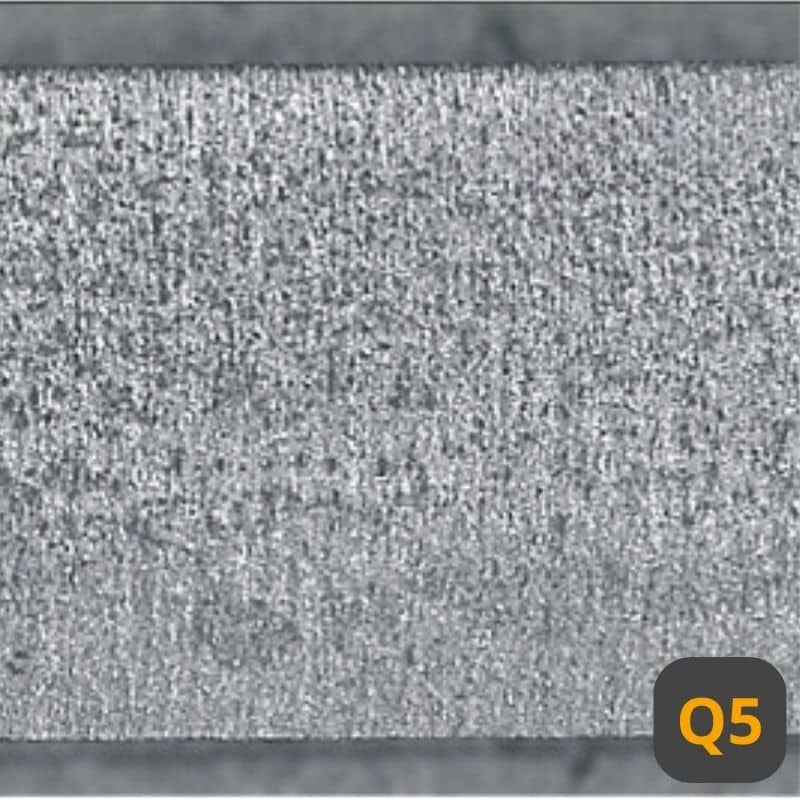
Cut Quality | Quality Class Description |
---|---|
Q1 | Rough cut, fast separation cut for rapidly processing parts. |
Q2 | Basic quality cut suitable for parts with minimal finishing requirements. |
Q3 | Standard quality cut used for general-purpose applications. |
Q4 | Fine-quality cut best for parts that will receive minimal post-processing. |
Q5 | Extra fine cuts reserved for applications that demand high precision and an excellent surface finish. |
The Extended Waterjet Cut Quality Classes (Q1-Q9)
As waterjet technology continued to advance, using fine waterjet cutting head to create jet diameters smaller than 0.5 mm (0.02 in.), it became clear that the traditional 5-level scale for waterjet cut quality classification was no longer sufficient to determine successful abrasive waterjet cutting.
Ultimately, the traditional edge quality classification scale could not accurately differentiate between the best cut quality obtainable with regular abrasive waterjet machines (AWJ) and the exceptional edge quality achieved with micro abrasive waterjet machines (MAW).
The nine classes of this new quality measurement scale range from Q1 for rough separating cuts, to Q9 for ultrafine cuts with parallel walls. The surface roughness of Q7 to Q9 cuts is relatively similar, meaning the biggest distinction between these classes is the conicity of the cut edges.
Micro Abrasive Waterjet Cut Quality Classes (Q1-Q9)
A Finecut micro abrasive waterjet machine can deliver any cut quality between Q1 and Q9 when cutting any type of material.
Cut quality | Quality Class Description | Application Examples |
---|---|---|
Q1-Q3 | Rough cut, fast separation cut for rapidly processing parts. | Ideal for rough cuts of scrap material or quick prototyping. |
Q4-Q6 | Intermediate quality cuts with improved surface finish. | Ideal for intermediate-quality cuts to save cost. |
Q7-Q9 | Highest precision cuts with minimal taper and smooth surfaces, where Q9 has totally parallel walls. | Ideal for high-precision cuts in aerospace, medical, and jewelry applications. |
As mentioned previously, waterjet cutting speed has a significant impact on cut quality. Lower cutting speed will result in a better edge quality, but when cutting speed get too low it will create an increased kerf angle.
What is also important to note is that higher cut quality classes require much lower cutting speeds which results in increased production time and cost. Therefore, it’s essential to balance cut quality with economic considerations.
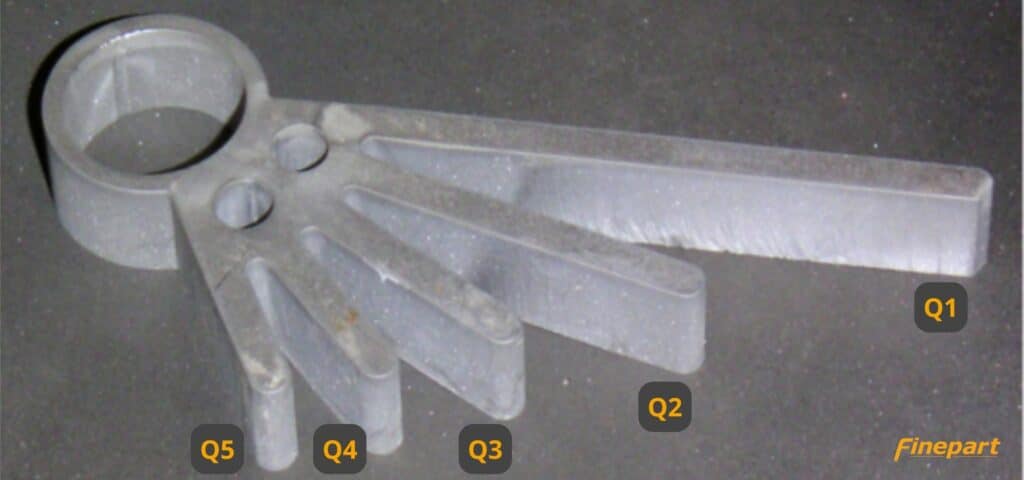
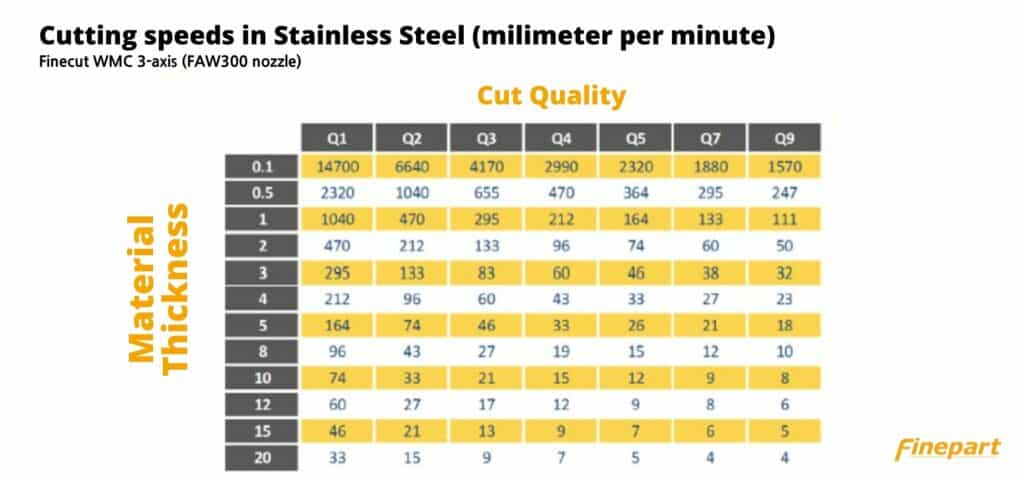
Factors Affecting Precision & Cut Quality
To understand the waterjet cut quality classification system, it’s useful to know the different factors that can influence cut quality. Here are some common elements that can affect waterjet quality outcomes:
- Water Pressure:
- Higher water pressure generally improves the edge quality because it creates a more clean cut with fewer rough edges. It enhances the cutting ability of the waterjet, which leads to better material removal and more smooth edges (Ahmed et al., 2018).
- Abrasive Type and Flow Rate:
- The type of abrasive and abrasive flow rate significantly impact edge quality. Abrasives like garnet, alumina, and silicon carbide each have different cutting efficiencies and will result in varying edge quality. Optimal abrasive flow rates will ensure effective cutting without excessive material removal that can reduce edge quality (Yu et al., 2020).
- Cutting Speed:
- Slower cutting speeds generally leads to higher edge quality because it allows a more precise material removal while also reducing the occurrence of striations and rough edges. However, too slow a speed can cause excessive wear on the nozzle (Thomas, 2009).
- Nozzle Distance (Stand-off Distance):
- The distance between the nozzle and the workpiece, known as stand-off distance, affects the jet’s focus and cutting power. Optimal nozzle distance ensures the jet remains concentrated and powerful, leading to cleaner cuts (Santhanakumar et al., 2015).
- Traverse Speed:
- The speed of nozzle as it moves across the workpiece influences the edge quality. If the traverse speed is too fast it can cause rough edges and striations, and if the nozzle speed is too slow it can lead to excessive material removal and roughness (Karakurt et al., 2012).
- Material Properties:
- The properties of the material being cut, such as hardness, density, and grain size, affect how the material responds to waterjet cutting. Harder materials require higher pressure and abrasive flow to achieve high edge quality (Kantola et al., 2013).
- Nozzle Condition:
- The condition and wear of the nozzle can significantly impact edge quality. Worn nozzles produce less focused jets, leading to poorer edge quality. Regular maintenance and replacement of nozzles are essential (Mostofa et al., 2010).
Each of these factors impacts waterjet precision and quality in a different way. For example:
Factor that influence cut quality | What you need to do | |
---|---|---|
1 | the cutting speed can influence surface roughness caused either by jet lag or taper. | Adjust the waterjet cutting speed to match the desired quality. |
2 | the purity, particle size and cleanliness of the abrasive can influence surface roughness | Use only premium abrasive recommended by the machine builder. |
3 | the diameter of the nozzle opening of the cutting head determines the size of striations that form | Adjust the waterjet cutting speed to match the desired quality. |
4 | the vibration in the part or the cutting tool can cause oscillation through the cut path | Use an appropriate workpiece fixture to eliminate vibrations |
The final surface profile on the part results from the combined influence of all the different sources of interference.
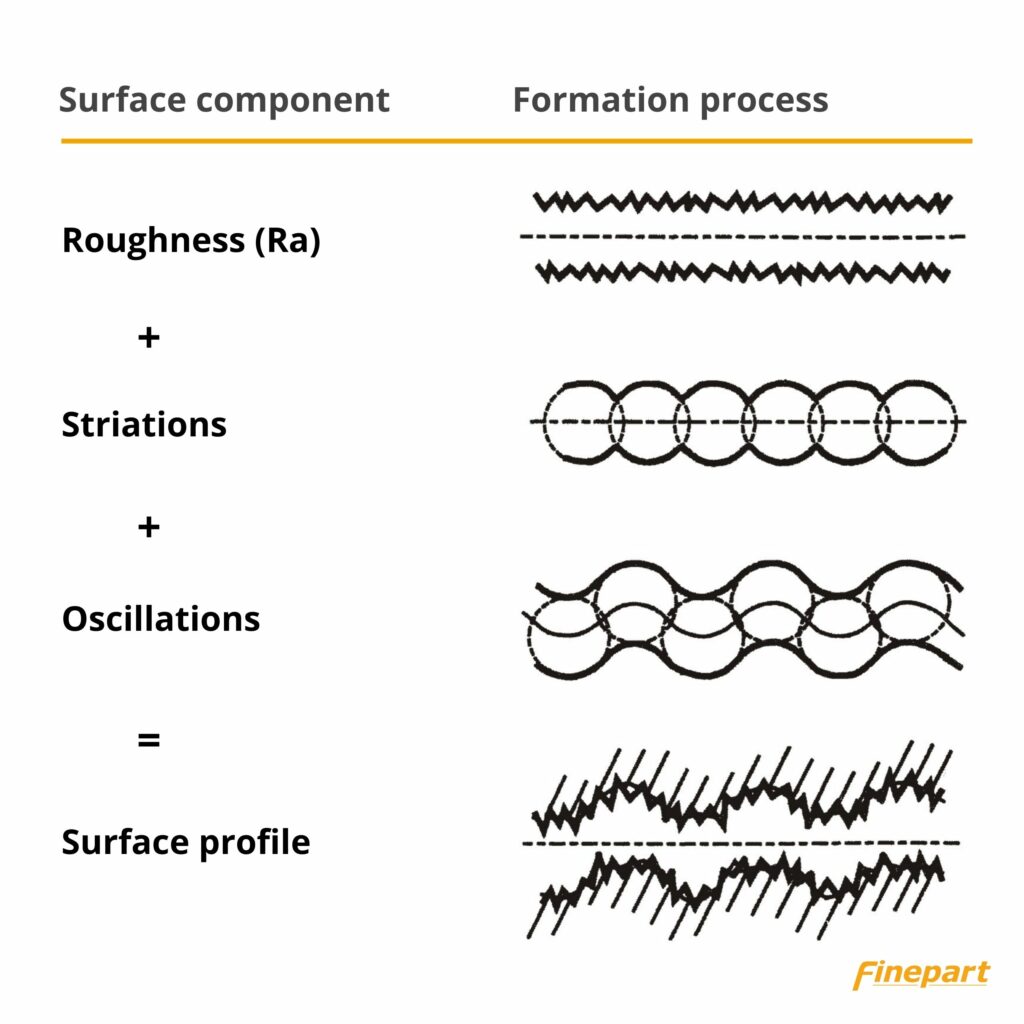
The final surface profile achieved by waterjet cutting a given material at a specific thickness can then be rated using the waterjet cut quality classification system.
Factors to consider when selecting the best cut quality
When a designer or fabricator is determining which cut quality class to use, they are essentially establishing a minimum acceptable quality standard that they have to achieve.
As highlighted in the tables listed above, a coarsely prototyped model and a medical device have very different requirements for the minimum acceptable finish quality.
To determine the ideal waterjet cut quality for a specific operation, it’s important to consider the following:
- The material type, as it is generally harder to get a good finish in softer materials.
- Application requirements, as the application may require a minimum acceptable finishing quality.
- Tolerances, as higher quality cuts will align with tighter tolerances.
- Budget, as higher quality classes require more processing time and better abrasive material that increase processes costs.
The CAD/CAM waterjet software in Finepart micro waterjet machines uses a built-in Zeng and Kim-style classification system to help operators quickly determine the best settings for specific cutting needs. As a result, it’s common for waterjet operators to send a cut quality sample to their customers so that they can best align cutting parameters with the client’s quality requirements.
Select the desired cut quality class for cost efficiency
Choosing a cut quality level too low for your application can result in defects, rejected parts, and dissatisfaction from customers. However, choosing anything higher than necessary decreases the production efficiency of your waterjet, effectively increasing your costs to produce those parts.
Ultimate surface quality with Finepart micro abrasive waterjet
For applications requiring the highest level of precision and finest surface finish, the Finepart micro abrasive waterjet is the ultimate solution. Finepart’s state-of-the-art waterjet precision cutting technology provides unparalleled cut quality, allowing you to achieve any desired quality level between Q1 and Q9. This allows for a broad range of applications, from rapid prototyping to creating highly intricate and refined designs.
Finepart micro abrasive waterjets bring you the versatility to succeed whether you need to prioritize cut quality, reap productivity benefits, or achieve a balance between the two.
BEYOND CUTTING EDGE
Finecut Micro Waterjet Series
The Finecut 3-axis, 4-axis, and 5-axis micro waterjet machine series for high precision cutting and ultimate surface quality
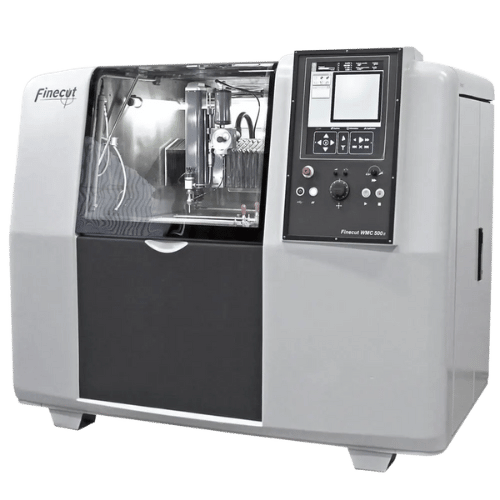