This article will cover waterjet cutting tolerances and explain the difference between waterjet accuracy and precision, describe the factors affecting these tolerances in waterjet cutting, and compare waterjet equipment with alternative cutting technologies.
“How accurately can a micro abrasive waterjet cut?” is an important question when evaluating a cutting machine. Just like knowing how much something costs or how fast it works, it’s important to understand the capabilities and limitations of the machinery you are considering working with. Determining the limits to the precision and accuracy of your equipment tells you whether it can meet the requirements of your projects.
Accuracy, Precision, and Tolerance in Waterjet Cutting
While they are sometimes used interchangeably, precision and accuracy are two different measures of machine performance. But both measures can be useful for describing how closely the cutting action aligns with design expectations.
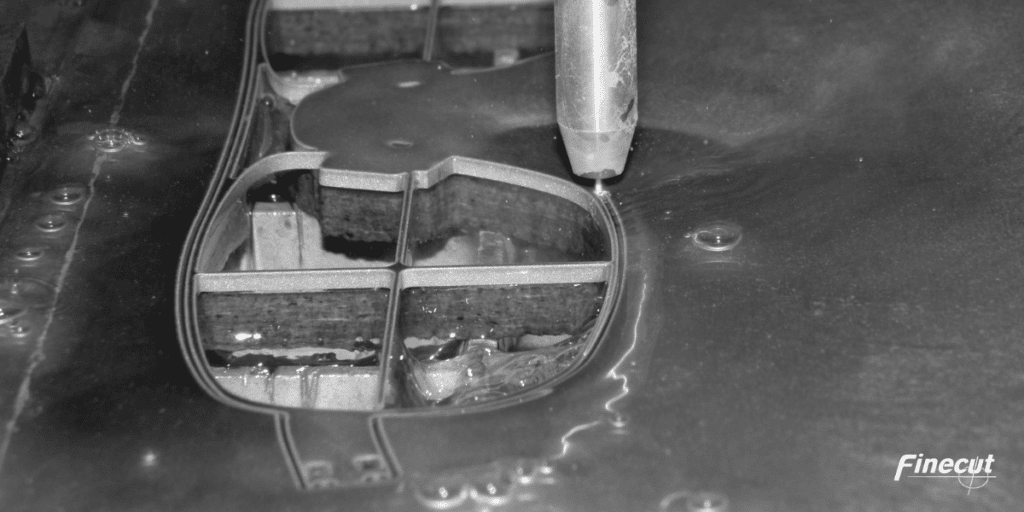
What is positioning accuracy?
In short, positioning accuracy is a representation of how accurately the waterjet machine can position itself. While cutting precision represents how much the final part differs from the design.
Positioning accuracy in waterjet machines is essentially the difference between where the machinery is supposed to be and where it actually is. A Finepart micro abrasive waterjet has very high accuracy and can carefully control the tooling to make cuts where intended. They demonstrate high repeatability, consistently meeting very tight tolerances.
What is repeatability?
Repeatability in waterjet cutting refers to the ability of a waterjet cutting machine to consistently produce identical cuts in the same material, under the same conditions, with the same parameters. This includes factors such as the precision and accuracy of the cutting head positioning, the consistency of the water pressure and flow rate, and the stability of the cutting process. Good repeatability is important for ensuring the quality and consistency of waterjet cut parts, especially in industrial and manufacturing settings where precision and accuracy are critical.
What is cutting precision?
So if positioning accuracy represents the waterjet “knowing” where it needs to cut and being in the right position, then cutting precision represents how closely the cuts made match the intended design.
How much the final result differs from an ideal cut line represents the degree of precision the waterjet can meet. A micro abrasive waterjet with high precision will cut patterns extremely close to the intended shape, while cuts made with worn or low-precision equipment may stray slightly further from the intended cut line.
The importance of accuracy
The result of inaccuracy in position could mean that a hole being cut through that part is slightly out of its intended position, and may render the part unusable and discarded in quality control. Hence the importance of accuracy as this means lost material, labour time, and machine utilization.
What is waterjet cutting tolerance?
Both accuracy and precision can be quantified by using tolerances. Tolerances represent the normal error or deviation from ideal performance. They are written as a distance with a “±” symbol and they are essentially the maximum amount you should expect the waterjet cutting machine or other CNC machines to deviate from perfect positional accuracy and perfect cutting precision.
Average waterjet tolerances
While it is highly dependent on the equipment being used, typical waterjet tolerance values for abrasive waterjet cutting machines are ±0.002 in. (0.05 mm) or greater.
A Finecut FAW 500II 5 axis micro abrasive waterjet has tolerances as tight as ± 0.0004 in. (0.01 mm).
In either case, errors on this scale are completely imperceptible to the human eye. Micro waterjet cutting machines generally have exceptional accuracy and precision, but these tolerances can vary substantially between manufacturers as it is dependent on both the software and the construction of different hardware components and the machine design.
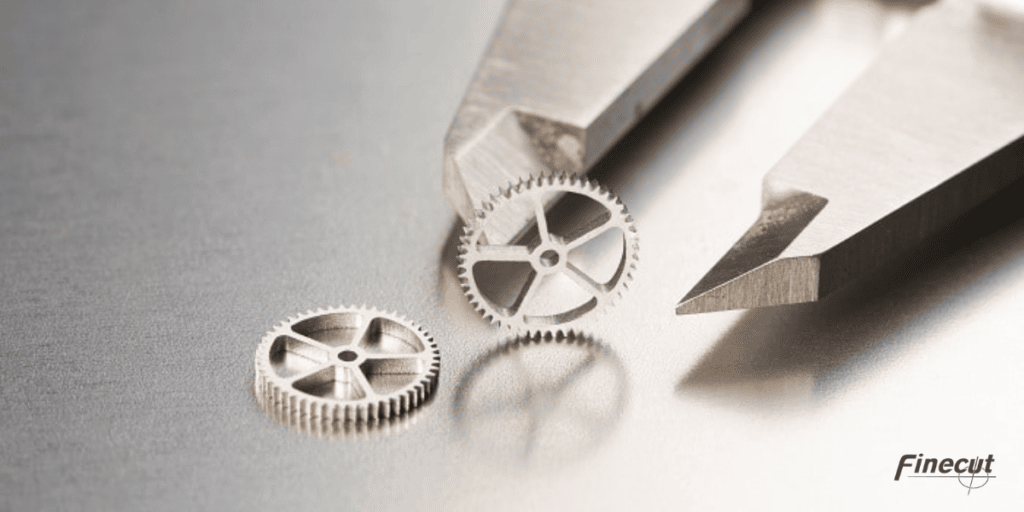
What Affects Waterjet Cutting Tolerances and Precision?
Positioning accuracy, stability, and equipment condition
As mentioned already, positioning accuracy is a measure of how reliably a waterjet can manipulate tooling and parts. Even though it can be evaluated on its own, it has a big impact on cutting precision. Proper positioning of the waterjet nozzle is an important part of ensuring the waterjet stream is directed where it should be, allowing for high-precision cuts.
Parameters to watch for
- Smallest radius
- Narrow passages
- Passage width in relation to jet diameter
- Material thickness
- Power / Speed requirements
Stability of cutting table
Along those lines, stability of the cutting table, fixturing used to hold parts in place, and even the part design itself are all essential to achieving tight tolerances in the cutting process. Vibration or deflection can lead to major inconsistencies. Regular servicing and maintenance of equipment can help keep your waterjet machine cutting at peak precision.
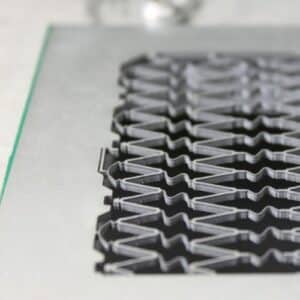
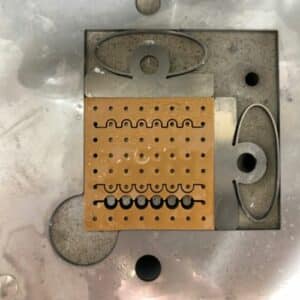
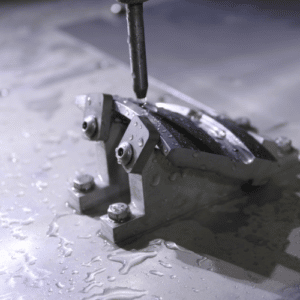

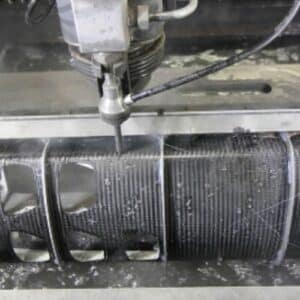
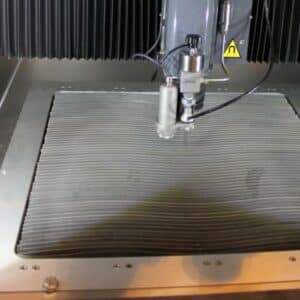
Abrasives quality
The abrasives used in the waterjet cutting process can impact the behaviour of the waterjet stream. While there are a number of different suitable abrasives, consistently sized and shaped abrasive particles will improve uniformity and precision. These are staple qualities of any waterjet abrasive material, or garnet.
Abrasive parameters influencing the cutting performance
- Material type (hardness, density)
- Mechanical behaviour (friability)
- Particle shape
- Particle size and size distribution
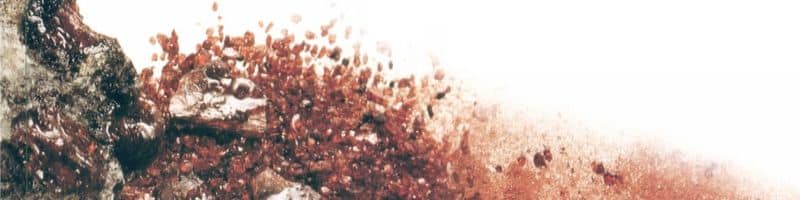
Cutting parameters
Cutting speeds, feed rates, pressures, and other operating parameters all have an impact on cutting tolerances. But unlike some of the other factors in this list, cutting parameters have to be optimized on a case-by-case basis. Reducing cutting speed alone may not improve precision. Parts with different designs that are made from different materials can behave in unpredictable ways. It make take some adjustment to optimize cutting parameters for precision in this case.
Workpiece qualities
A waterjet machine is suitable for a wide range of different workpieces, including a range of materials and part thicknesses. Different materials can exhibit different behaviors during cutting, so the best results come from adjusting your cutting process to accommodate the part. Generally speaking, material hardness has a big impact on precision as softer materials will experience more taper during cutting. The thickness that the waterjet stream needs to penetrate also affects the cut edge and therefore also the tolerances.
Waterjet software and waterjet CNC controllers
The software and controllers used by a manufacturer can potentially have a significant impact on cutting precision. Higher quality controllers and software from a reputable manufacturer will lead to tighter tolerances as it is capable of following the intended cutting path more accurately.
Machine operator experience
The experience of the machine operator can have a substantial impact on the results of the waterjet cutting process. Skilled operators can adjust for material thickness and hardness, optimize cutting parameters, and account for other factors that effect accuracy and precision. Knowledge about fixturing is also essential when you are aiming for high tolerances.
Accuracy of Micro Abrasive Waterjet Technology vs Other Cutting Methods
Modern cutting methods offer producers a wide range of solutions, each with their own benefits and shortcomings. For the most part though, modern CNC cutting processes are highly accurate, with tolerances ranging from okay to exceptionally good. The following popular processes are listed from most precise to least precise.
Cutting Technology | Precision mm | Precision inch |
---|---|---|
Wire EDM | ±0.0025 mm | ±0.0001” |
Femtosecond Laser | ±0.001 mm | ±0.00004″ |
Micro Abrasive Waterjet | ±0.01 mm | ±0.0004” |
Abrasive Waterjet | ±0.1 mm | ±0.004” |
Laser | ±0.1 mm | ±0.004” |
Plasma | ±0.5 mm | ±0.002” |
While wire EDM and femtosecond lasers offer the highest precision in this list, their other drawbacks may make them unsuitable for a range of cutting operations and materials. Likewise, while plasma cutting has at least 10x the tolerance range of other methods, it stills sees use in many machine shops as a cost effective solution for rough cuts. Evaluating precision tolerances is just one aspect of choosing the best machinery for your application.
Finecut FAW 500II, 5-Axis Micro Abrasive Waterjet
Probably the most accurate micro abrasive waterjet in the World.
The Finecut 5 axis micro waterjet is at the cutting edge of precision cutting, edge quality, and cutting speed. So if precision, quality, and speed are important to you. A Finecut FAW 500II is possibly the best choice among micro abrasive waterjets.
Cutting tolerance specifications for Finecut 5-axis micro abrasive waterjet:
- Positioning accuracy*: ± 2.5 µm 0.0025 mm (0.00001″)
- Repeatability*: ± 2 µm 0.002 mm (0.00008″)
- Typical cutting tolerance ± 10 µm 0.01 mm (0.0004″)
- Max cutting speed: 20 m/min (65.6 ft./min)
- Max traverse speed: 40 m/min (131.2 ft./min)
BEYOND CUTTING EDGE
The Ultimate In Waterjet Precision Cutting
Micro abrasive waterjet series, the ideal technology for advanced cutting in virtually any material.
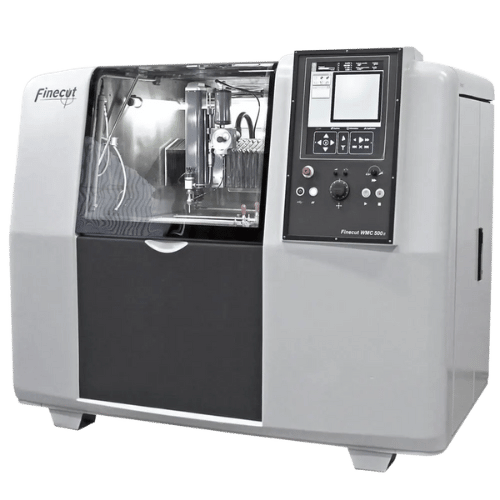