In this article we cover how micro abrasive waterjet cutting stainless steel can provide high precision and surface quality. Stainless steel is a popular metal for all kinds of applications because of its high strength, great corrosion resistance, and reasonable cost for raw material. But what many product developers may not realize is that it can be tricky to cut or machine stainless steel and obtain high-quality results.
How to cut stainless steel with high precision and surface quality?
Using a micro abrasive waterjet for cutting stainless steel is probably the most versatile and reliable way to achieve high-quality, accurate results with minimal material waste and a reduced need for secondary operations. This article gives insight into the reasons stainless steel is hard to cut, the benefits and drawbacks of precision cutting methods, and how to cut stainless steel effectively.
Examples: Precision Cutting Stainless Steel
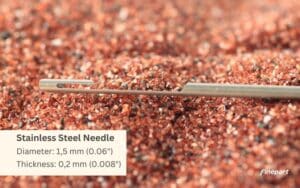
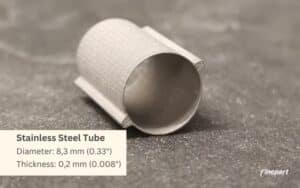
Challenges of Cutting Stainless Steel
Here are the main challenges operators face when precision cutting stainless steel:
1. Mechanical properties
Relatively speaking, stainless steel is very hard, quite tough, and has a tendency to work harden when cold worked. While this often makes stainless steel very durable and valuable for a wide range of applications, it can make precision cutting very challenging. They can cause increased tool wear, a poor surface finish, and difficulty meeting tight tolerances requirements. This is especially the case when cutting and machining feed rates are low.
2. Heat generation and management
Stainless steel has a lower thermal conductivity, which means the heat generated during the cutting process can quickly build up in a localized area. In some cases, this can lead to thermal expansion and distortion in the material that affects cut precision.
Alternatively, if the heat build-up is severe enough at the surface of the stainless steel it can cause sensitization of the metal’s surface or the formation of a heat-affected zone. Sensitization of stainless steels means significantly decreased corrosion performance and greater susceptibility to stress corrosion cracking (SCC).
The formation of a heat-affected zone on the stainless steel can also mean reduced ductility and microcracking. Choosing non-thermal cutting methods like waterjet can help mitigate this issue.
Methods for Precision Cutting Stainless Steel
While there are many different methods for cutting stainless steel, there are only a handful that can consistently produce high-quality, precise cuts.
Plasma cutters, oxy-fuel cutters, shearing, and other similar methods do not have the versatility or precision to create high-quality cuts. Using a plasma cutter or oxy-fuel cutter in particular will result in very rough edges and a large heat-affected zone (HAZ) near the cutting line.
As a result, conventional machining, laser cutting, and abrasive waterjet cutting are the most useful cutting methods for stainless steel applications.
Conventional machining & sawing
Sawing uses a high-speed, toothed blade to cut through stainless steel. A circular saw or band saws with the appropriate blades designed for cutting stainless steel can be used for this purpose. Saws can produce somewhat clean cuts, but they can generally only create straight-line cuts across the entire cut path and would need grinding and polishing to improve the surface finish.
Traditional milling, lathing, and drilling are more suitable for intricate designs and high-precision applications. They can potentially create a very good surface finish and have the advantage of being able to accurately cut curves and partial-thickness features.
Traditional machining methods also frequently use coolants applied directly to the cut location to help manage temperature and minimize work hardening in stainless steels. They may also need to use specialized carbide tooling or a diamond blade to prevent excessive tool wear, as dull tools can increase the work hardening of stainless steel.
Unfortunately, for stainless steel sheets and plates that require a lot of intricate detail, conventional CNC machining is much slower than laser or waterjet cutting. Machining also cannot achieve the level of complexity or intricacy possible with the other two cutting methods due to limitations on the kerf width that can be achieved.
Laser cutting stainless steel
Laser cutting uses a high-powered laser beam to cut through stainless steel by melting and vaporizing the material. This method leads to high precision and clean edges, but it can also generate heat that may result in an unwanted heat-affected zone or sensitization of the stainless steel.
Laser cutting is suitable for various thicknesses, though micro waterjet cutting can handle thicker sheets, and cutting thicker materials requires a more powerful laser cutter.
Micro abrasive waterjet cutting stainless steel
Abrasive waterjet technology uses a highly pressurized stream of water mixed with abrasive particles to cut through stainless steel.
Micro abrasive waterjet is the next evolution of this cutting technology, using finer abrasive particles and a more advanced focusing nozzle to create kerf widths of 0.2 to 0.5 mm.
The micro abrasive waterjet method produces very clean, smooth edges and does not pass heat stress onto the workpiece, even when cutting thick stainless steel sheets. This makes it ideal for applications requiring high precision, an excellent surface finish, and consistent metallurgical properties.
Waterjet cutting can handle a wide range of material thicknesses and ensures the material properties of the workpiece are not compromised by uncontrolled heating and cooling from a thermal cutting process.
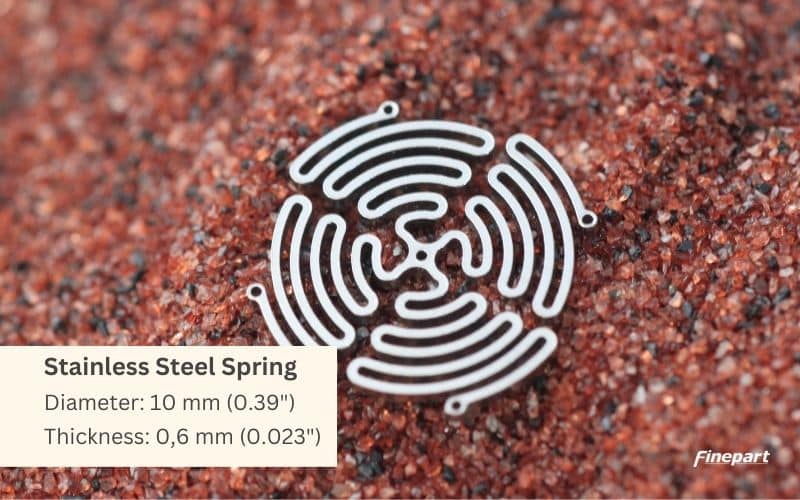
Best Practices for Waterjet Cutting Stainless Steels
Micro abrasive waterjet machinery is an invaluable tool for high precision, non-thermal cutting of stainless steel. Waterjet operators can get a better idea of how to cut stainless steel with superior results by following a few key tips:
Step 1 – Use a precision waterjet machine
Invest in a high-quality micro waterjet machine that has a fine nozzle and is designed for high precision cutting.
The Finepart micro abrasive waterjet machine technology utilize nozzles that can focus the high-pressure water stream to a 0.2 – 0.3 mm diameter. They also have a precise and stable motion control system that allows the work surface to be accurately positioned within ±0.0025 mm (2.5 microns).
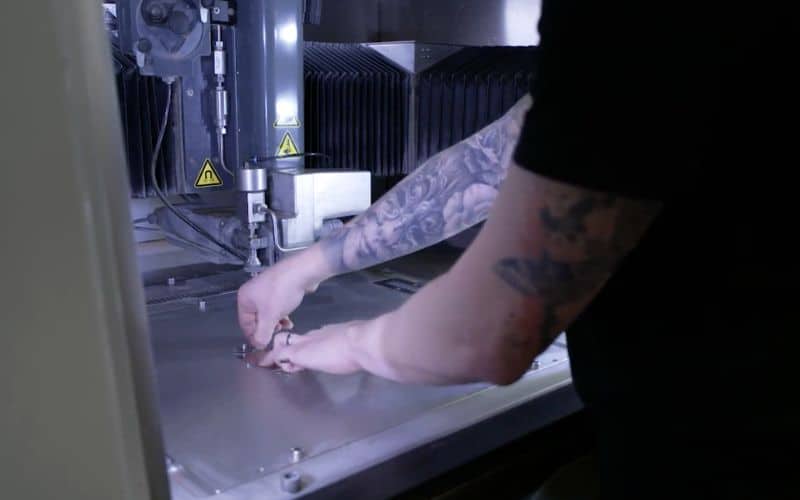
Step 2 – Clean and prepare the stainless steel
Clean the surface of the stainless steel to remove any dirt, debris, or grease. Place the stainless steel sheet on the waterjet cutting table, ensuring it is flat and well-supported to avoid unwanted deflection.
The stainless steel sheet should be properly secured to prevent movement during the cutting process.
Step 3 – Set up the machine carefully
Import the cutting plan into the waterjet control software. Set the machine’s parameters, including the water pressure, abrasive flow rate, and cutting speed. These parameters depend on the thickness of the stainless steel and the desired cut quality.
Intelligent software, like the IGEMS software in Finepart machines, can assist operators with determining, water pressure, tolerances, cutting speed, and how to cut stainless steel precisely every time.
Step 4 – Perform test cuts
It’s a good idea to perform a test cut on a scrap piece of similar stainless steel alloy before you start cutting stainless steel products. This will help you determine if the machine settings need any adjustment so that you know exactly how to cut stainless steel on the real production run.
Step 5 – Monitor the process
Keep an eye on the cutting process to ensure there are no issues or deviations from the cutting plan. If necessary, make adjustments to the machine parameters to optimize the cutting quality and precision.
Step 6 – Clean the finished piece
Once the cutting process is complete, including any optional finishing passes, remove the stainless steel piece from the cutting table.
Clean the cut edges using a deburring tool or fine-grit sandpaper to remove any remaining abrasive particles or sharp edges.
Step 7 – Inspect the final product
Examine the cut edges and overall quality of the stainless steel piece. Ensure that the cuts are clean, accurate, and meet the desired level of precision.
If necessary, make adjustments to the machine settings and repeat the process to achieve the desired result.
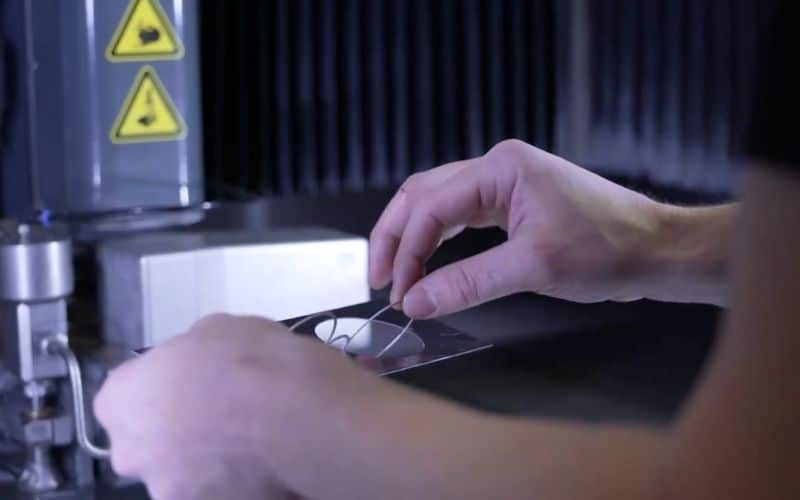
What Are The Benefits of Precision Cutting Stainless Steel With a Micro Waterjet?
Micro abrasive waterjet machines offer several important advantages over other cutting methods when producers need to cut stainless steel.
High precision and accuracy
Micro waterjet cutting can produce intricate designs and complex shapes within tight tolerances.
Finepart machines specifically can cut features with an accuracy of ±0.01 mm (10 microns) at the part level, making them perfectly suited for applications that require an ultra-high level of precision.
This level of precision is much better than the ±0.1 mm (100 microns) offered by most standard laser cutting equipment. Femtosecond laser equipment can achieve even better accuracy but is only suitable for materials less than 1 mm thick.
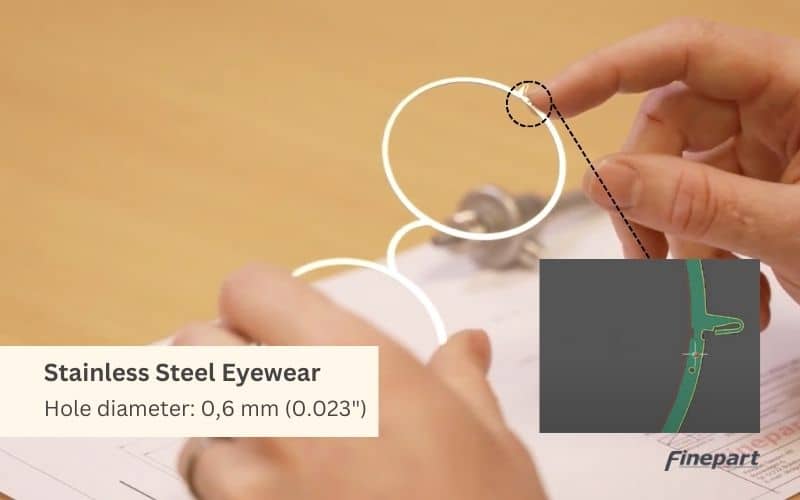
No heat-affected zone (HAZ) or sensitization
Micro waterjet cutting is a cold cutting process, which means it doesn’t generate heat that could alter the material’s properties.
This eliminates the risks of a heat-affected zone forming along the cut line, heat warping or distortion of delicate features, and significant microstructural changes in the stainless steel.
It also means significantly fewer microcracks formed during processing and consistent corrosion resistance across the stainless steel part.
Smooth and clean edges
The micro waterjet cutting process produces clean edges with very minimal burr formation. This typically means that waterjet-cut stainless steel requires little to no additional finishing or deburring. This reduces the need for secondary operations and can save time and labor costs.
Using a Finepart 3 axis or 5 axis micro waterjet when cutting steel means the cut can be done in a single pass with a second, optional finishing pass only needed for improving the surface finish further.
Minimal kerf width
The thin kerf width of the micro waterjet stream (0.2 mm to 0.3 mm) results in minimal material waste, making it an efficient cutting method for expensive materials like stainless steel.
The easy-to-use software of Finecut micro waterjet machines also tackles challenges related to kerf taper for thick stainless steel materials, adjusting cutting parameters to ensure an even thickness and high precision.
Great versatility and high penetration
Micro waterjet can cut stainless steel efficiently for a wide range of thicknesses and alloy compositions, including thick stainless steel alloys with relatively high hardness values. In fact, Finecut micro abrasive waterjets can handle stainless steel sheets up to 30 mm thick. This versatility allows for more design freedom and flexibility in manufacturing for both stainless steels and other materials.
BEYOND CUTTING EDGE
Finecut Micro Waterjet Series
Easy to operate 3, 4, and 5 axis micro waterjet machinery for high precision cutting stainless steel parts with ultimate edge and surface finish in one single process.
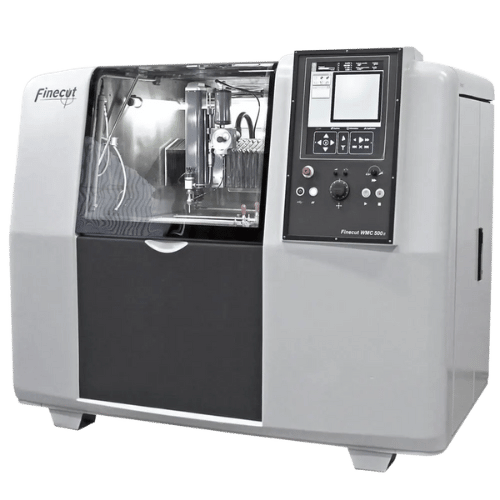