This article will explain what micro abrasive waterjet machining and cutting is and how modern advancements compare against traditional cutting methods.
The idea of waterjet cutting has been around since the 1800s in one form or another. But relatively recent advances in technology have propelled this cutting method to the forefront of the manufacturing and processing industries. This is largely thanks to the extremely precise capabilities of micro abrasive waterjet machining and cutting.
Examples of micro abrasive waterjet cutting
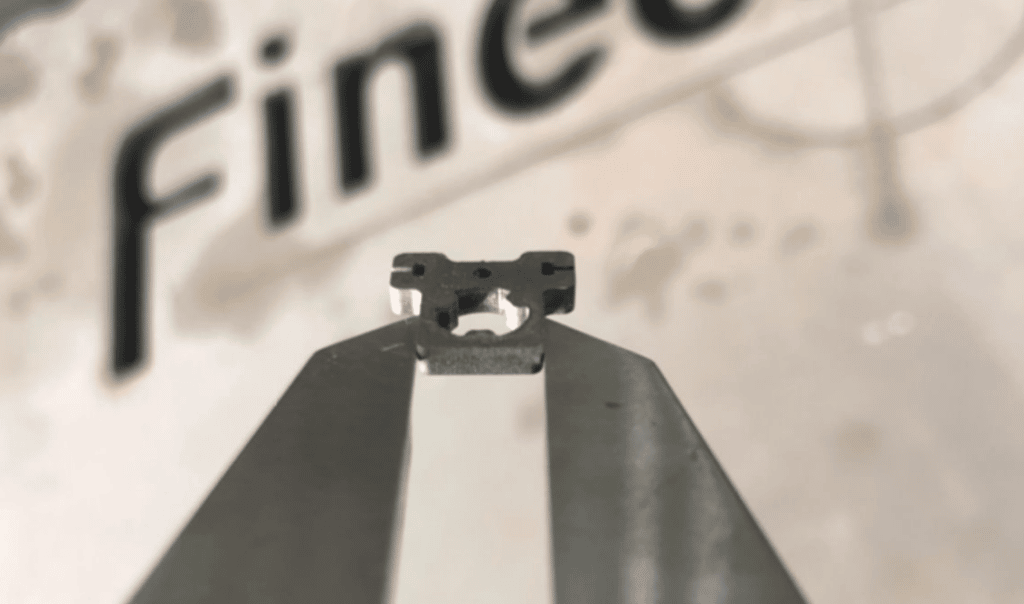
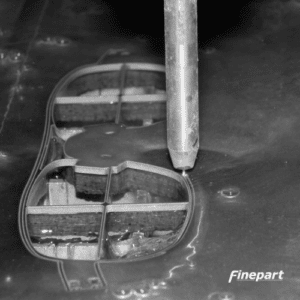
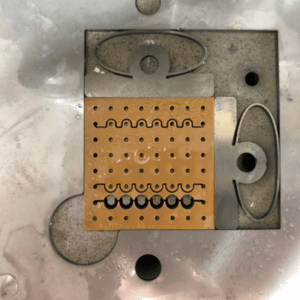
What Is Micro Abrasive Waterjet Cutting & Machining?
Simply put, Micro Abrasive Waterjet (MAW) uses a narrow, high-pressure jet of water with hard particles of abrasive material to cut or machine parts. Waterjet is one of few cutting and machining tools that doesn’t introduce any heat into the workpiece material. And thanks to the use of abrasive grains, it can be used to cut virtually any material as long as the abrasive is harder than the workpiece materials.
While waterjet machining is incredibly efficient and versatile, current technology can only be used reliably for full-thickness cutting. It cannot perform partial-thickness cutting in the sense that a femtosecond laser and milling machine can create a slot or pocket in a workpiece without fully penetrating through to the other side. To some extent you can use MAW for ablation or marking, but it is difficult to precisely control the depth of the cut. While this does restrict the applications of waterjet machining somewhat, waterjet machines with multiple-axis capabilities can still cut angled features similar to femtosecond laser and wire electrical discharge machining (wire EDM).
Micro abrasive waterjet cuts virtually any material
The use of waterjets with an abrasive material for cutting metals and other hard materials is actually a relatively recent advancement. Originally, waterjet cutting machines used a simple jet of pressurized water to cut paper and other soft materials. This was known as pure waterjet cutting. But after researchers included abrasive material in the waterjet, they developed a distinct process called abrasive waterjet (AWJ) cutting that could cut hard materials.
Cold cutting technology with no heat affected zones
Thanks largely to how efficiently it could cut metals without creating a heat-affected zone, AWJ boosted the value and popularity of waterjet technology. Then as waterjet technology continued to advance, researchers and engineers improved the design. One key aspect included reducing the focusing nozzle diameter until a much narrower jet stream was produced. Previously, the best abrasive waterjet cutting equipment could achieve a kerf width of 0.5 mm, and today some Micro Abrasive Waterjet cutting systems even goes down to 0.2 mm. Development for even smaller jet diameter is ongoing.
Adding Abrasives: The 2 Main Abrasive Waterjet Methods
Abrasive Water Injector Jet (AWIJ)
Adding an abrasive significantly increases cutting power over pure waterjet cutting, and there are currently two popular methods for doing this. The first is abrasive water injector jet (AWIJ) cutting, which is defined by the dry abrasive material being pulled into the already-pressurized water stream in a mixing chamber thanks to the Venturi effect. The high-pressure abrasive water injector jet accelerates the abrasive in a focusing nozzle which then exits the nozzle toward the workpiece surface.
Abrasive Water Suspension Jet (AWSJ)
Abrasive water suspension jet (AWSJ) cutting can be a slightly more efficient approach where the water is first compressed using a high-pressure pump and then mixed with the abrasive to form a slurry in the absence of air. This has the benefit of accelerating the abrasive grains more efficiently than AWIJ, which can mean faster cutting at similar water pressures. One downside however is that the abrasive water suspension jet cutting process is normally batch-based, so this may result in more frequent stoppages to replenish the abrasives in the equipment.
The Differences Between Pure Waterjet, AWJ & MAW?
The progression of waterjet technology from pure waterjet cutting to AWJ and then MAW has led to a significant expansion in the capabilities of abrasive waterjet cutting as a whole. But all 3 methods are still widely used today for different applications where each is best suited.
Material compatibilities & thicknesses
With a lower cutting power, pure waterjet cutting is well-suited for cutting soft materials. This includes materials like rubber, paper, styrofoam, cardboard, and nearly anything else with similarly low hardness values. It generally works best on thinner stock as well, and can even cut some metal foils if they are thin enough.
Abrasive waterjet machining and micro abrasive waterjet machines can cut much harder and thicker materials, ranging from softer metals, like aluminum, up to very hard materials, like carbon fiber and titanium alloys. The thickness range is dependent on the material used but micro abrasive waterjets (MAW) can accommodate thicknesses up to 20 mm (0.8″) and beyond.
As a result, when evaluating abrasive vs pure waterjet based on material options, many people may be quick to think that an abrasive solution is always better. However, while abrasive waterjets are capable of cutting softer materials as well, the high cutting forces may deform the material around the cut line. For this reason, we cannot simply say that AWJ and MAW are the explicitly better choices as pure waterjet cutting machines will still have value when dealing with certain soft and thin materials.
Cutting speeds
Generally speaking, the abrasive in AWJ improves cutting speeds over pure waterjet cutting while Micro Abrasive Waterjet machining focuses more on precision and edge quality still being much faster than pure waterjet. That said, cutting speed is also highly dependent on the material you’re working with, the abrasives being used, and the capabilities of the individual equipment.
Finepart micro abrasive waterjet cuttings speed
MAW is divided into 9 different cut quality classes where Q1 is just a separating cut and Q9 is the highest quality. Q9 only has about 10% of the speed of Q1. Which speed you can use depends to a very large extent on what quality you want on the cut and what cutting tolerance and precision you wish to achieve. If you cut 5-axis, the cutting speed can be increased significantly. The table below shows cutting speeds for 3-axis cutting with a water jet that is 300 microns in diameter.
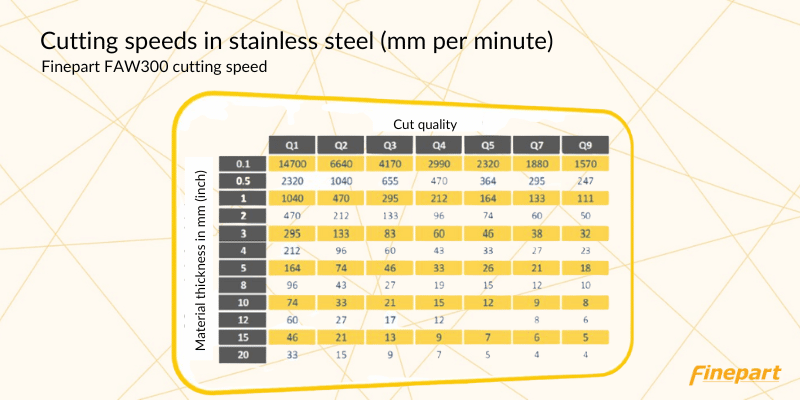
Cutting accuracy & tolerances
A large part of accuracy is related to the choices of OEMs in terms of machine design, waterjet software, waterjet CNC controllers, and even the quality & precision of parts. This also means that newer, more modern equipment can generally reach tighter cutting tolerances. Broadly speaking though, modern pure waterjets and micro abrasive waterjet machines are designed for machining finer details, so they can typically create more accurate results.
Cutting Technology | Precision mm | Precision inch |
---|---|---|
Wire EDM | ±0.0025 mm | ±0.0001” |
Femtosecond Laser | ±0.013 mm | ±0.0005” |
Micro Abrasive Waterjet | ±0.01 mm | ±0.0004” |
Abrasive Waterjet | ±0.1 mm | ±0.004” |
Laser | ±0.1 mm | ±0.004” |
Plasma | ±0.5 mm | ±0.002” |
Kerf size and complex cutting capabilities
Their narrower jet streams give pure waterjet cutting and MAW machines a smaller kerf width. This means they can create finer details and more complex designs than traditional abrasive waterjet machining. Kerf size is also the main differentiator between AWJ and MAW when it comes to defining what makes an abrasive waterjet “micro”.
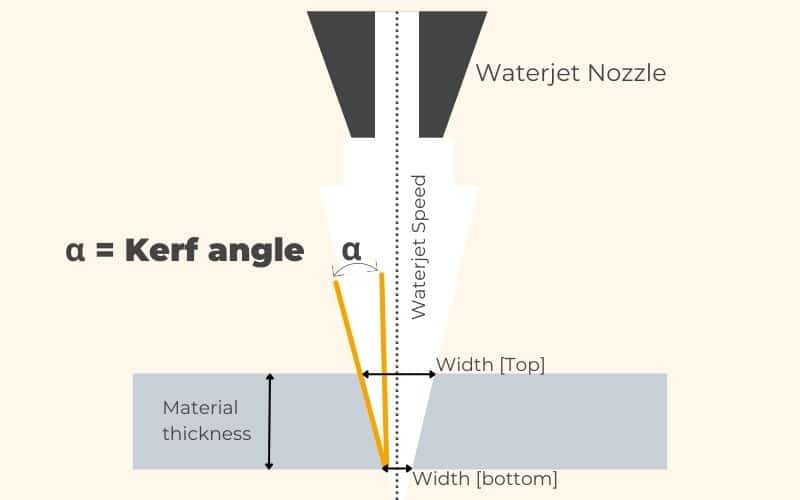
Operating cost
One of the biggest costs of operating waterjet equipment is maintaining a regular supply of high-quality abrasive grains. For this reason, a pure waterjet cutting machine is generally the cheapest to operate of the 3 waterjet technologies. MAW generally requires a higher quality abrasive than AWJ, so this can slightly increase its material supply cost, however, the narrower stream consumes much less water and abrasive material. This means that the typical operational cost per hour is quite equal for traditional waterjet and MAW, but cutting power and speed is generally higher for the traditional abrasive water jet machines.
Sustainability
Overall, waterjet cutting technologies have the potential to be relatively sustainable and their biggest challenge is waste management. In many cases, pure waterjet cutting machines can filter workpiece fragments out of the waste fluid and reuse the water. AWJ and MAW on the other hand require more advanced equipment to filter the debris and abrasives out of the waste fluid. But for companies willing to purchase the necessary equipment and spend the time recycling waste material, they can also improve their sustainability.
Micro abrasive water jet machining also consumes less water than AWJ, so you can expect to have a lower cost to run with less water waste.
Ideal Applications for Micro Abrasive Waterjets
While MAW and AWJ both have higher cutting power thanks to their abrasive material, the precision and level of detail that can be achieved with Micro Abrasive Waterjet cutting sets it ahead. And while modern pure waterjet cutting machines can achieve a comparable level of detail to micro abrasive waterjets, they are most useful for thin, soft materials and cannot cut thicker or harder material.
As a result, MAW cutting process has the distinct advantage of delivering exceptional high precision cutting capabilities in a wide range of materials and thicknesses. This is in addition to the assortment of other benefits that waterjet cutting has over other machining processes, like fewer airborne dust particles, not imparting thermal stresses into the workpiece, and more.
In summary, micro waterjet cutting has potential in any number of industry applications, like:
- Automotive and robotics parts
- Heat & contamination-sensitive aerospace components
- Medical devices made from advanced materials
- Electronics components
- Consumer products
BEYOND CUTTING EDGE
The Ultimate In Waterjet Precision Cutting
Finepart micro abrasive waterjet series, the ideal technology for advanced cutting in virtually any material.
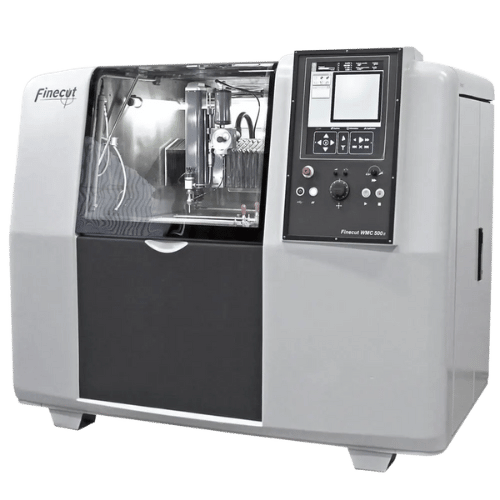