Waterjet is an excellent tool for precision cutting carbon fiber and virtually all other composites, including popular materials like fiberglass, Nylon and Kevlar. Using micro abrasive waterjet cutting machinery takes this to the next level, cutting composites and high-quality parts with ultra-high precision.
Capable of achieving an exceptionally small kerf and omnidirectional cutting capabilities, micro abrasive waterjet allows producers to cut incredibly fine details, even in tight spaces, using only a SINGLE cutting pass. And thanks to its non-thermal operation, intricate cutting concentrated within a localized area will not overheat and damage materials like carbon fiber reinforced plastic (CFRP). This prevents the kind of material distortion seen in heat-affected zones that result from other cutting methods used on carbon fiber, like milling, saws, and lasers.
Key Takeaway: Abrasive waterjet cutting improves hole quality and reduces tensile strength in CFRP laminates, while pure waterjet cutting causes surface defects and increases tensile strength1 (Maojun Li & Mingjie Huang & Xujing Yang & Shuo Li & Kai Wei, August 2018).
In this article, you will find a guide to the best way to cut carbon fiber, how to avoid delamination and an overview of the advantages and disadvantages of cutting CFRP and other composites using micro abrasive waterjet.
The Challenges of Cutting Composites (CFRP, CRP, GFRP, GRP)
Depending on the intended application, carbon fiber products may be subjected to a number of different forming and processing steps, including cutting, drilling, and machining, among others. In this sense, the excellent materials properties of CFRP can, unfortunately, become a challenge, making product development more difficult when compared to alternative materials like aluminum sheet or fiberglass.
Using poor technique with any common cutting method can cause the carbon fiber to:
- Overheat (thermal damage) and even melt the plastic matrix, deforming the workpiece.
- Burr and fray, which increases tooling time, damages cut edges, and compromises cut line precision.
- Release carbon dust, which can be harmful to exposed personnel and electronic equipment.
- Delaminate, compromising both the integrity and appearance of the product.
- Absorb contaminants when unsuitable coolants and lubricants are applied to the cutting area.
If even one of these cutting issues occurs, it can compromise your expensive carbon fiber product. This may simply mean poor aesthetics, or it could compromise the integrity or dimensional accuracy of your product.
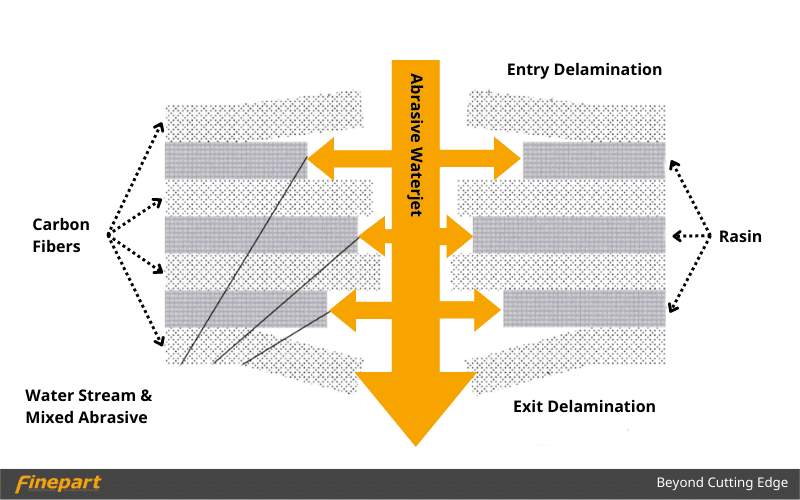
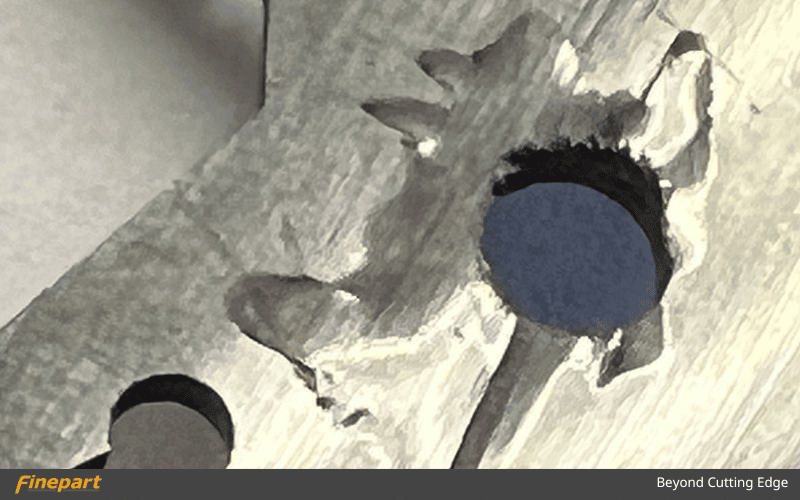
Cutting Composites with Waterjet
With micro abrasive waterjet machining, you can complete complex ultra-high precision cutting, increase productivity, reduce material and labor costs, avoid microcracks or fiber pull, and eliminate delamination.
Avoiding Delamination
Delamination of carbon fiber during waterjet cutting typically happens when the waterjet is first piercing holes through the material. With nowhere to go during the first penetration, the high-pressure waterjet cuts through each resin layer with ease, but the tough carbon fibers redirect part of the waterjet stream perpendicular to the cutting direction. This can start eating away the resin matrix between the layers of woven carbon fiber, causing delamination and making the material unusable.
The solution is to either pre-drill starting holes into the composite, or to pierce holes using careful control of the waterjet properties.
Predrilling and piercing with Finecut’s micro abrasive waterjet
Cutting holes in carbon fiber
Piercing new holes using a micro abrasive waterjet requires careful control of both water pressure and abrasive feed to ensure pressurized water does not hit the carbon fiber before the abrasives2 (Ioan Alexandru Popan, Nicolae Bâlc, Alina Ioana Popan August 2021). Using this method, you may want to increase the feed rate and lower the water pressure to ensure that the abrasive feed hits the surface first or at the same time as the water to avoid delamination.
Whether you are cutting in lower or higher quality CFRPs there is always a risk of delamination when piercing the initial hole in the material. So the easiest way to eliminate the risk of delamination is to predrill the hole with a waterjet machine that provides an integrated waterjet cutting head and high frequency spindle unit for drilling. This eliminates misalignment and means the predrilling and cutting happens on the same machine in one process.
With a Finecut micro abrasive waterjet the feed is automatically controlled to ensure that the abrasives hit the surface at exactly the same time as the water stream, to ensure a piercing without delamination. If predrilling is a preferred option, Finecut can be equipped with an integrated drill and high-speed spindle, which means drilling and cutting is done in the same process and ensures perfect alignment in any cut.
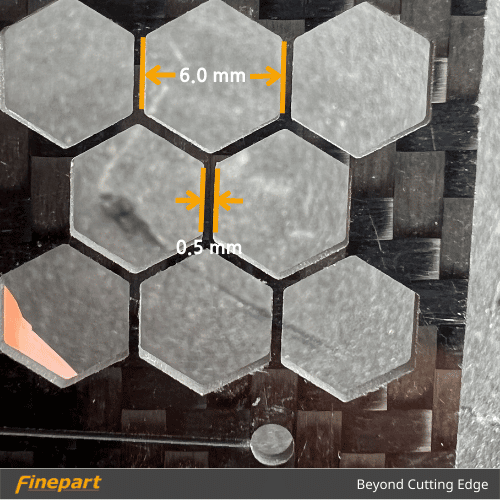
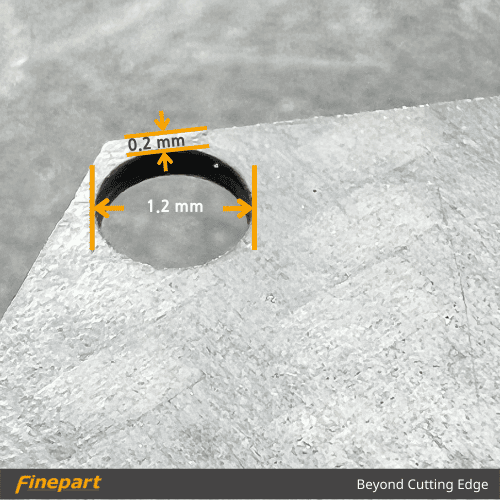
Eliminating taper
When cutting thicker composite materials you may see some taper develop through the thickness of the cut. The taper can be adjusted by:
- Speeding up or slowing down the pressure and feed rate.
- Adjusting the abrasive feed volume.
- Adjusting the angle of the nozzle or using a multi-axis cutting head control system.
- Adjusting the distance of the nozzle from the material.
With a micro abrasive waterjet like the Finecut 5 axis micro waterjet, the tilting, distance from the material, and feed rate are optimized for you via the automated control system.
Ultimate edge finish
Because a waterjet uses an abrasive to cut through the strong carbon fibers, you may have a slightly rough edge surface.
To fix this you can easily use a finer abrasive and adjust the feed rate to achieve the perfect edge quality. The finer the abrasive, the finer the finish!
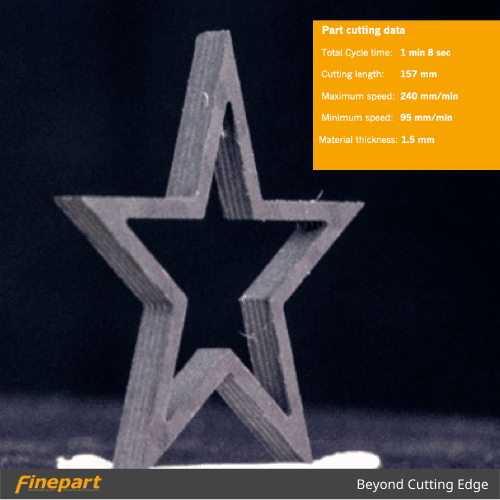
Benefits of Cutting Carbon Fiber Using Micro Waterjet Machining
Abrasive waterjet technology is the best way to cut carbon fiber and other composite materials. And if you are looking to fabricate smaller, more complex carbon fiber shapes and maintain a high -quality edge finish, micro abrasive waterjet technology is really your only option.
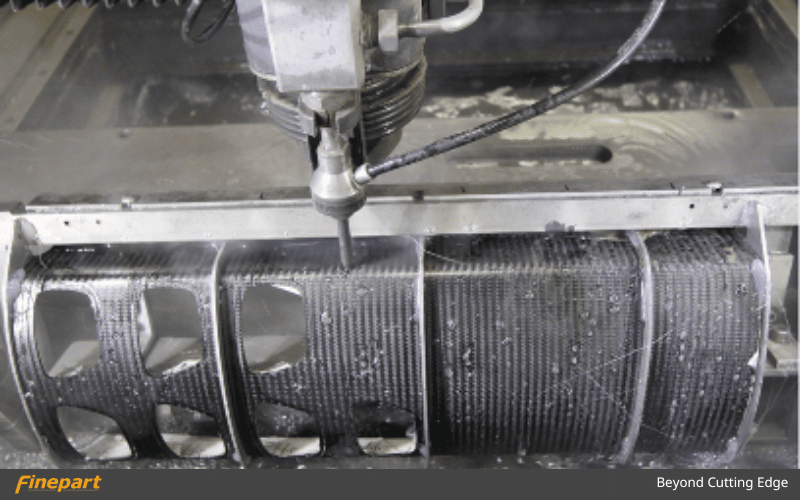
Micro abrasive waterjet cutting offers benefits over a number of other cutting methods in the following areas.
Flexibility in material thickness
A major advantage of micro abrasive waterjet technology is that it can cut both very thick and very thin carbon panels with ease, often in one passing depending on material thickness. This saves you production time, lowers labor costs, and reduces material waste.
Finecut Micro Abrasive Waterjet Machines // Materials that a waterjet can cut
Fast cutting of high-quality parts in one passing
A micro waterjet can easily cut small, complex 3D carbon fiber parts that would be impossible with a conventional waterjet cutting process. This means reduced processing times thanks to the high cutting speeds of the Finecut micro abrasive waterjet machinery.
Minimal kerf
Kerf can impact the level of detail a cutting method is able to achieve. Micro waterjet allows you to produce 3D cut shapes with incredible detail and minimal kerf thickness for ultimate precision.
Finepart Academy: All about kerf & taper in waterjet cutting
No thermal damage and heat-affected zones
Waterjet is a cold cutting technology, which eliminates the risk of heat-affected zones and material distortion.
Little or no need for a second edge finish
While there is a risk of rough edges, when using a micro abrasive waterjet, this can be controlled with the garnet mesh size (the finer the abrasive, the finer the finish) and the feed rate. This leads to a smoother finish with no need for a second pass and no delamination in most composite materials.
Easy carbon fiber dust containment
Carbon fiber dust can easily find its way into the inner workings of your machines and cause parts to wear faster than normal. It is also a health hazard as the dust can cause irritation in the eyes, lungs, and itchiness if it gets on your skin. A waterjet machine automatically contains the dust using the water jet stream, containing dust in the water tank. This can then be easily filtered out and eliminates the need for air pressure and air filtration systems.
Choosing Finecut Micro Waterjet Machinery By Finepart
The Finecut-series of micro abrasive waterjet machines align with our pioneering mission to push the boundaries of what waterjet systems are capable of. Finepart is dedicated to bringing you the highest precision cutting waterjet technology, quality products and services to meet your waterjet cutting needs.
BEYOND CUTTING EDGE
The Ultimate In Waterjet Precision Cutting
Finepart micro abrasive waterjet series, the ideal technology for advanced cutting in virtually any material.
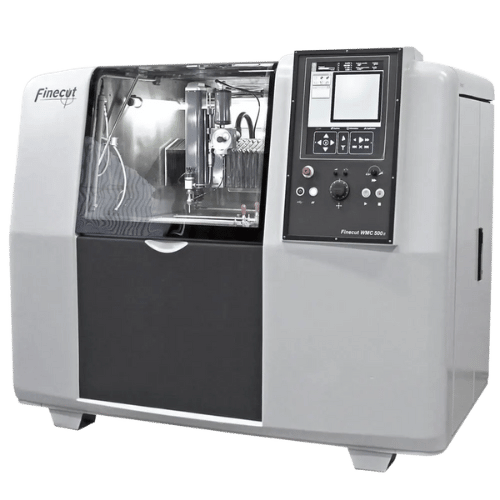
References:
- Maojun Li & Mingjie Huang & Xujing Yang & Shuo Li & Kai Wei (2015). Experimental study on hole quality and its impact on tensile behavior
following pure and abrasive waterjet cutting of plain woven
CFRP laminates.
↩︎
Ioan Alexandru Popan, Nicolae Bâlc, Alina Ioana Popan (August 2021). Avoiding CFRP Delamination During Abrasive Water Jet Piercing: A New Piercing Method ↩︎ - ↩︎
FAQ