This article discusses what Nitinol is, why machining and cutting Nitinol is so difficult, and why micro abrasive waterjet cutting is the preferred method for cutting it.
If you need a material with high biocompatibility, superelastic properties, or the ability to “remember” and revert to a specific shape, you are probably considering using Nitinol. This amazing material can be used for a number of unique applications thanks to its peculiar material properties.
While these special characteristics make Nitinol an invaluable material, they are also part of the reason Nitinol cutting and machining is so challenging.
What is Nitinol (Nickel Titanium)?
In the following we have provided a brief explanation on why Waterjet Cutting Nitinol is ideal for cutting nitinol, and provides the highest level of production capabilities, precision, cutting speed, and surface quality in one single pass.
Nitinol –
Nickel-Titanium alloy discovered at the Naval Ordnance Laboratory
Nitinol’s superelasticity, or pseudoelasticity, means that it can be stretched past the limits of other metals that would permanently deform or break under similar conditions. This means it can be used for applications like orthodontic wires in dentistry, that continuously shrink after placement so that they don’t need to be readjusted. Or they can be used in civil engineering applications to make damping or “self-healing” concrete structures.
Shape memory alloy
The ability of Nitinol products to remember their original shape means they can shrink if stretched and then reheated, applying tension as it shrinks. But it also allows for other complex applications. As a shape memory alloy, Nitinol alloys can be bent, twisted, and stretched, then returned to its desired shape with moderate heating. Even the heat produced from a human body is enough to trigger the shape memory effect (SME). Along with its high corrosion resistance and biocompatibility, this makes Nitinol an excellent material for medical devices like nitinol stents.
Why is nitinol hard to machine?
While Nitinol offers some excellent product capabilities, it is also a very difficult-to-machine alloy for two main reasons. First off, Nitinol is a very hard material because of the titanium oxide layer that forms on its surface. The high hardness means large cutting forces are needed to deform or remove material, and mechanical tools used for cutting quickly become dull and worn. If you need to cut tiny Nitinol with shear-type cutters, or if you need to machine larger Nitinol workpieces with a CNC lathe or milling machine, expect high tool wear and frequent tool replacement.
Managing heat input
The second major challenge of machining or cutting Nitinol is managing heat input during processing. Because of its properties as an SMA, Nitinol is sensitive to these thermal stresses, which can damage its ability to achieve the shape memory effect. Any thermal cutting process, like laser cutting or Wire EDM, introduces a heat-affected zone (HAZ) adjacent to the cut area, part of which has been heated above the maximum allowable temperature for the Nitinol to retain its abilities as an SMA. For parts cut using thermal processes like laser, the HAZ may need to be removed by other non-thermal machining methods after initial cutting.
Avoiding material distortion
For small features, there is a risk that thermally-based cutting can affect Nitinol’s shape memory properties through the part’s thickness. On the flip side, cutting thicker parts with laser cutting means slower cutting speeds and higher heat input in a localized area. Turning and milling generate significant heat and cause material distortion. Wire EDM provides slightly better results than turning and milling, but far from the quality that femtosecond laser and micro abrasive waterjet can deliver.
Overall, managing heat input is one key area where cold cutting methods like micro abrasive waterjet cutting have a distinct advantage. This makes cutting nitinol more efficient, easier to do, and more cost-effective when using micro abrasive waterjet.
Precision cutting nitinol with micro abrasive waterjet
In this video you will see how a Finepart micro abrasive waterjet cuts nitinol surgery clips without any need for a second finish, all in one cutting process
The Finepart micro waterjets is a cold cutting process that provides exceptional high precision cutting capabilities of complex shapes, optimum cut quality, high cutting speeds, and low production costs.

Examples of Micro Waterjet Cutting Nitinol
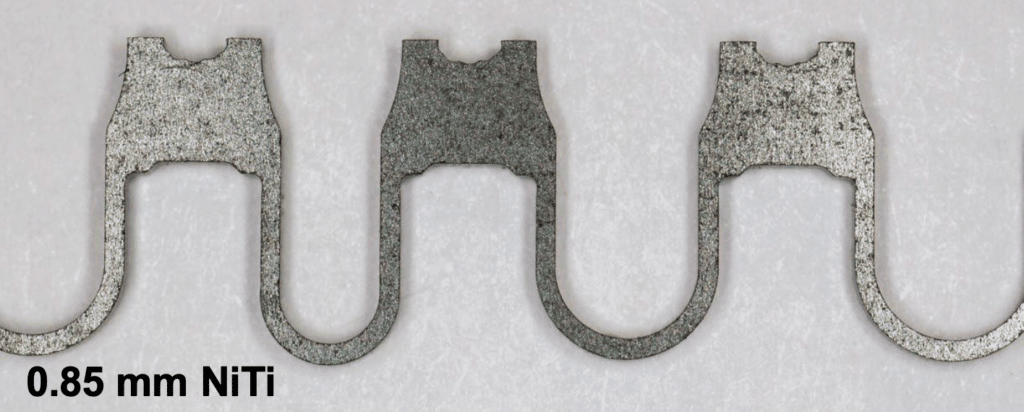
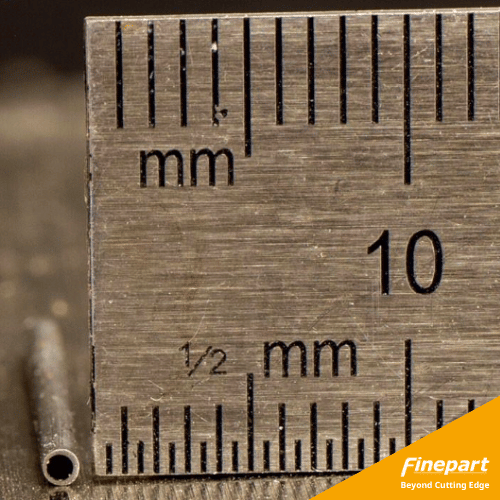
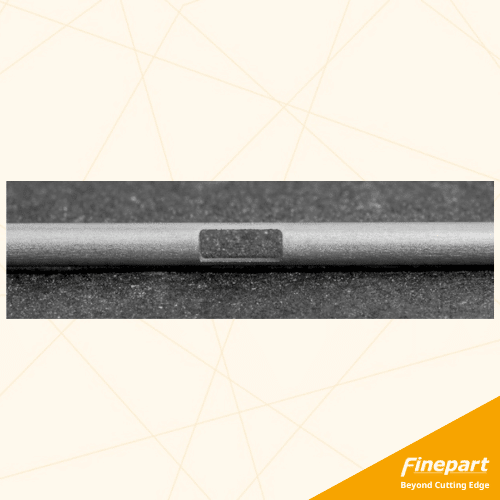
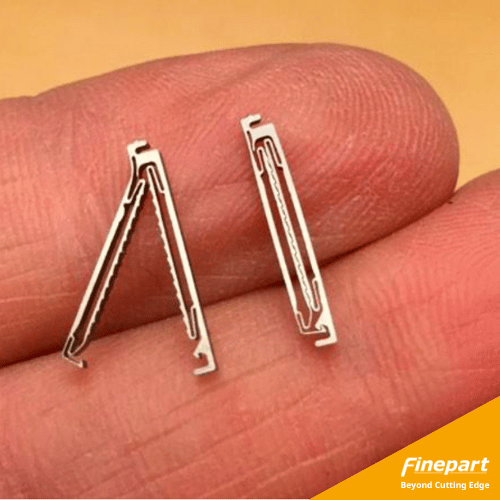
What is nitinol used for?
Nitinol has been around since the early 1960s but was unavailable commercially until twenty years later due to the tight controls needed in the manufacturing process. Since then, it has become an important material for robotics and in the medical industry for various medical applications, like medical devices. Nitinol is superelastic (10X as flexible as other metals), and its thermal shape memory properties are unlike any other material available.
Nitinol Applications: Medical Devices
- Dentistry, especially in orthodontics for wires and brackets that connect the teeth.
- Endodontics, mainly during root canals for cleaning and shaping root canals.
- In colorectal surgery, the material is used in various devices for reconnecting the intestine after a pathology is removed.
- Nitinol Stents
- Surgical implants and surgical instruments
- Orthopedic implants.
- Medical guidewires
- Nitinol screws
- Nitinol wire
- Nitinol stent
- Nitinol tube
- Surgical implant
Other industries and applications that utilize nitinol parts include:
- Frames for glasses
- Cell phone components
- Temperature controls
- Mechanical watch springs
- Energy/power related applications
- And many more!
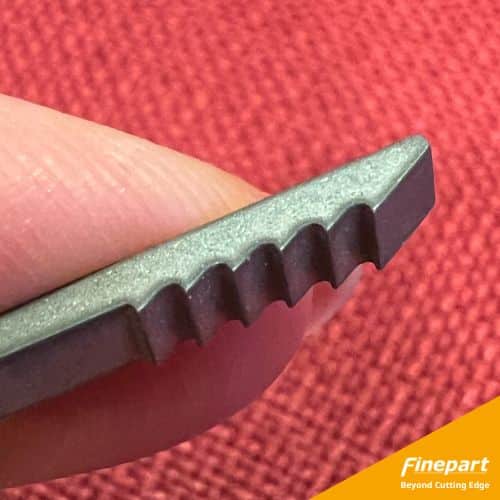
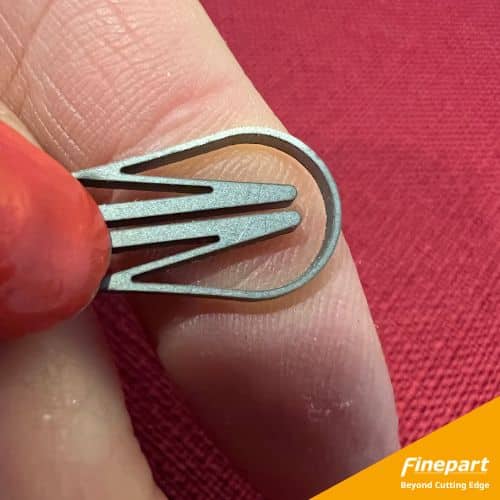
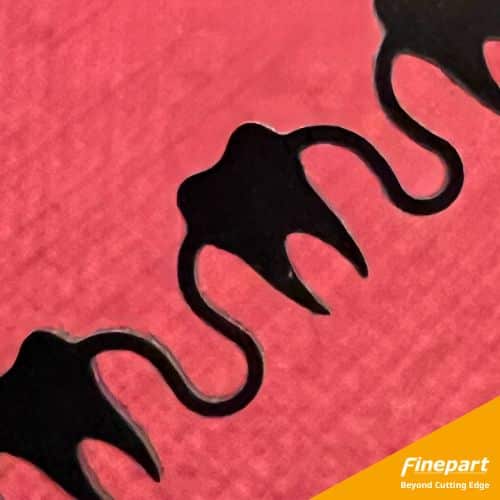
Choosing the Best Micro Waterjet For Your Needs
To find out which micro waterjet machines will fit your requirements best, you should make your decision based on the following factors:
Finecut Series of
Micro Abrasive Waterjets
3 axis, 4 axis, and 5 axis micro waterjet series, the ideal technology for cutting nitinol.
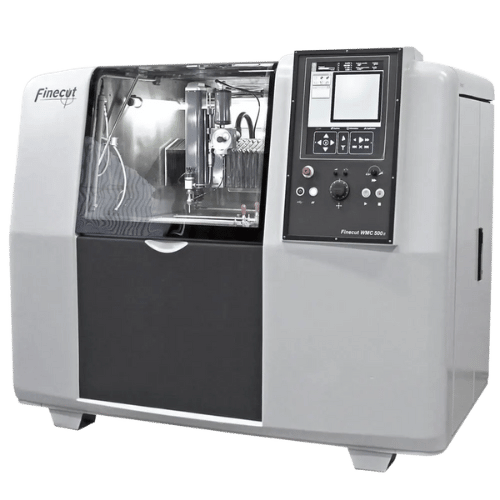