Micro abrasive waterjet vs EDM (Electrical Discharge Machining) cutting are not fundamentally new technologies, but recent advancements have significantly improved their capabilities. These machining methods can cut with greater precision and speed than they ever could before, making them essential additions to top machine shops around the world.
How do EDM & micro waterjet compare?
In this article, we’ll provide an overview of wire EDM and micro abrasive waterjet cutting, evaluating their precision, surface quality, productivity, capabilities, and usage restrictions. This head-to-head comparison will give you insight into the best use case for each technology and explain how they complement each other.
What is the difference between micro abrasive waterjet vs EDM cutting?
Wire-EDM cutting
Wire electrical discharge machining, often shortened to wire EDM or even W-EDM, is a unique process used to machine electrically conductive materials. While being constantly flushed with a dielectric solution of deionized water, the workpiece and the EDM wire are subjected to a voltage difference that turns them into electrodes. When the two electrodes are near enough to each other, the large difference in electrical potential between them causes the deionized water to temporarily experience a localized dielectric breakdown, becoming momentarily conductive. When this happens, the extremely high current jumps between the EDM wire and the workpiece, causing a powerful spark that removes a tiny fragment of both electrodes. And since the thin EDM wire is also damaged by this spark, a constant supply of fresh wire must be fed through the machine.
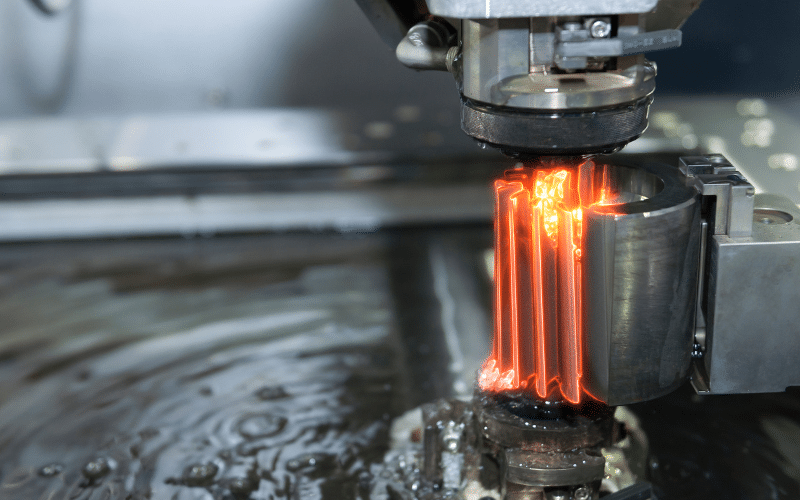
EDM cutting sparks occur hundreds of thousands of times per second, which is where the nickname “spark machining” comes from. While the primary removal mechanism of EDM is not fully agreed on, the EDM wire never directly contacts the workpiece, but the sparks generate an extremely high temperature comparable to welding that creates a small heat-affected zone adjacent to the cut path. On a microscopic level, the “high points” of the workpiece act as the lowest resistance path through the dielectric, meaning they are removed first. This result is that all the roughness “peaks” are largely eliminated, especially on finishing passes, which can create an impressively smooth surface.
Micro Abrasive Waterjet Cutting
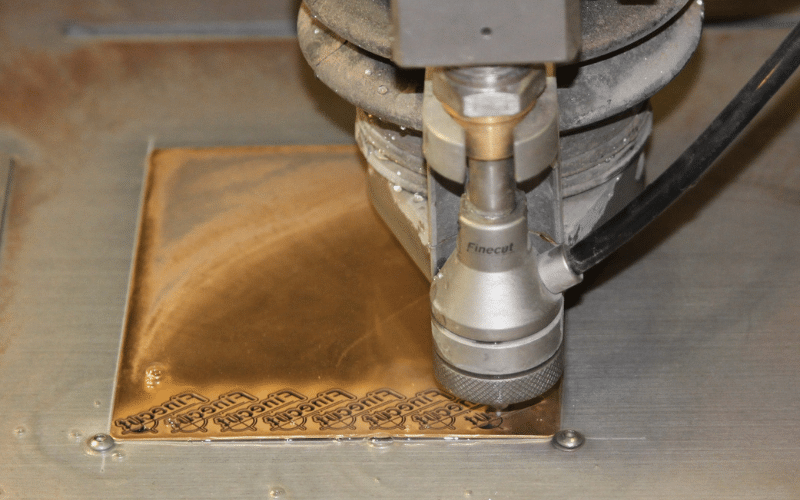
Traditional abrasive waterjet cutting process uses a stream of highly pressurized water to accelerate hard abrasive particles through a focusing nozzle directed at a workpiece. The jet stream erodes the material it impacts, effectively cutting through it as the high-pressure water and particulates impact the workpiece.
Micro abrasive waterjet technology is the latest advancement in waterjet cutting, reducing the diameter of the jet stream and the abrasive particles to create an ultra-precise cutting tool. This also significantly improves both the edge finish and surface finish it can achieve over traditional waterjet. So the micro abrasive waterjet can achieve cutting tolerances and surface finishes that astound those only familiar with traditional waterjet capabilities. And in terms of cutting speed, micro abrasive waterjet cutting is still around 5 to 10 times faster than EDM, though this depends on a myriad of factors.
The exceptional performance of micro abrasive waterjet cutting puts it in direct competition with a number of other high-precision machining methods, such a femtosecond laser cutting, but with the advantage of higher productivity, a wider range of suitable materials, and no detrimental heat-related effects.
Read: Micro Waterjet vs Laser cutting (femtosecond laser)
Micro Abrasive Waterjet vs EDM – Which is the best cutting technology for you?
Selecting the right cutting technology is important for your part quality and parts cost and therefore you need to consider your needs for each of the specific factors mentioned here:
Cutting Tolerance & Accuracy
Tolerance and accuracy is fundamental for the level of repeatable part quality that you produce.
Micro Abrasive Waterjet | Wire EDM |
---|---|
± 10 µm | ±2.5 µm |
Cutting Speed & Productivity
Micro Abrasive Waterjet | Wire EDM |
---|---|
Highly dependent on the workpiece parameters, but an average speed of 30-300 mm (1.2″-11.8″) per min for most common applications. | Highly dependent on the workpiece parameters, but often 5-10x slower than waterjet. |
Surface finish
Micro Abrasive Waterjet | Wire EDM |
---|---|
Very good. Ra around 1-2μm. Reduced speed and finer grit can improve surface finish. | Very good. Ra around 1-4 μm after a single pass. |
Heat-Related Effects
Micro Abrasive Waterjet | Wire EDM |
---|---|
None. Cold-cutting technology with no heat affected zone. | Formation of visible heat-affected zones and recast layer. |
Micro cracks and burr
Micro Abrasive Waterjet | Wire EDM |
---|---|
Micro cracks: The risk of micro cracks is minimal in the case of micro abrasive waterjet cutting. This is because the process is non thermal and particle impingement creates a compressive stress in the top surface. | Micro cracks: Wire-EDM uses a thin wire and electrical discharges to cut through material. This process generates heat which can cause micro cracks in the cut material, especially in hard and brittle materials. |
Burr formation: Burr formation is minimal to non-existent with micro abrasive waterjet cutting. The process leaves a clean edge and is less likely to create burrs due to the fine abrasive particles and the absence of heat. Soft materials, e.g. plastics, can exhibit minor burr. | Burr formation: Wire-EDM is more likely to cause burr formation due to the heat generated during the cutting process, which can cause material to melt and re-solidify but can often be minimized with proper process control and parameters. |
Maximum Cutting Thickness
Micro Abrasive Waterjet | Wire EDM |
---|---|
Appr. 30 mm (1.18″), depending on tolerance requirement and nozzle combination thicker materials are also possible. | Machine dependent, but over 300 mm (11.8″) can be achieved. |
Material that can be cut
Micro Abrasive Waterjet | Wire EDM |
---|---|
Micro abrasive waterjet systems are capable to cutting materials of any kind, including compound materials, non-conductive materials, as well as reflective or translucent materials that e.g. lasers are unable to. | Wire EDM machines have the restriction of cutting only conductive materials like metals and graphite, and require the material to be relatively homogenous. |
Main Consumables Costs
Micro Abrasive Waterjet | Wire EDM |
---|---|
Abrasive feed and replacement of worn nozzles & orifices. | Wire and electrode replacements. Filters. |
Energy Consumption
Micro Abrasive Waterjet | Wire EDM |
---|---|
~8-20 kW (depending on nozzle configuration) | ~15 kW |
Cutting Comparison Chart: Abrasive Waterjet vs Wire EDM cutting
In summary, here is a short comparison of some key factors for both micro abrasive waterjet and wire EDM.
Factor | Micro Abrasive Waterjet | Wire EDM |
---|---|---|
Main Consumables Costs | Abrasive feed and replacement of worn nozzles & orifices. | Wire and electrode replacements. |
Energy Consumption | ~8-20 KW | ~15 KW |
Cutting Speed & Productivity | Highly dependent on the workpiece parameters, but an average speed of 30-300mm (1.2″-11.8″) per min for most common applications. | Highly dependent on the workpiece parameters, but often 5-10x slower than waterjet. |
Material that can be cut | Can cut through almost anything. Cuts through both conductive and nonconductive materials. | Can only cut through materials that are both electrically conductive and relatively homogenous. |
Maximum Cutting Thickness | 30 mm (1.18″) | Machine dependent, but over 300 mm (11.8″) can be achieved. |
Cutting Tolerance & Accuracy | ±10 µm | ±2.5 µm |
Kerf Width | 0.2-0.4 mm (0.008″-0.16″) | Typically, 0.2-0.32 mm (0.008″-0.013″) but depends on the wire used. |
Surface finish | Very good. Ra around 1-2 μm after a single pass. | Very good. Ra around 1-4 μm after a single pass. |
Heat-Related Effects | None | Formation of visible heat-affected zones. |
Micro cracks | minimal to non-existent | Likely to cause micro cracks caused by heat |
Burr | minimal to non-existent | Likely to cause burr caused by heat |
The Conclusion micro waterjet vs wEDM
Both W-EDM and micro abrasive waterjet cutting are precision cutting tools that provide essential capabilities to fabricators around the world. As you may have guessed, the different capabilities of these two methods make them ideal for fundamentally different applications.
W-EDM – Ultrathick cuts of conductive materials with high precision
W-EDM is a niche process that works best for extremely thick, conductive materials and parts that need the absolute highest level of precision. It produces a very good finish for many of the materials it can cut and excels at machining a number of hard metals. And this performance can often be improved by using high-quality EDM consumables. Often, thinner materials can be stacked and several details can be cut at the same time.
However, because of its comparatively slow processing times, it is better suited to low production runs of high-performance parts. Overall, this makes W-EDM an essential tool for many aerospace organizations and research teams to produce the highly complex, precise, and unique parts they need for their fields.
Abrasive waterjet – Unmatched versatility, complex precision cutting and speed
The ability of micro abrasive waterjet cutting to cut material of virtually any kind within tight tolerances and to produce excellent surface properties makes it incredibly useful to a growing number of industry applications. While it is limited to working with parts thinner than 30mm at the cut location, micro abrasive waterjet has a distinct advantage as a rapid, non-thermal cutting process. Its high throughput and moderate cost to operate make it a worthwhile addition to a variety of cutting service shops, which is one of the key reasons for its surging popularity.
Finepart Micro Waterjets – Beyond Cutting Edge
The leading manufacturer of high precision micro abrasive waterjets
Considering Finecut micro abrasive waterjet cutting machines as an addition to a W-EDM shop’s machine tool inventory can offer various advantages. These machines can cut non-conductive parts efficiently, enabling businesses to broaden their scope of operations while keeping running costs moderate. The ability to pierce and cut precise parts in the same setup with higher cutting speeds can result in economic benefits, particularly for thin parts. Additionally, while these machines are excellent for cutting aluminum and precious metals, they are also effective for advanced engineered metals like Nitinol, magnesium alloys, and titanium without the need for dealing with recast layers or heat-affected zones.
BEYOND CUTTING EDGE
Finecut Micro Waterjet Series
Easy to operate 3, 4, and 5 axis micro waterjet machinery for high precision cutting advanced material parts with ultimate edge and surface finish in one single process.
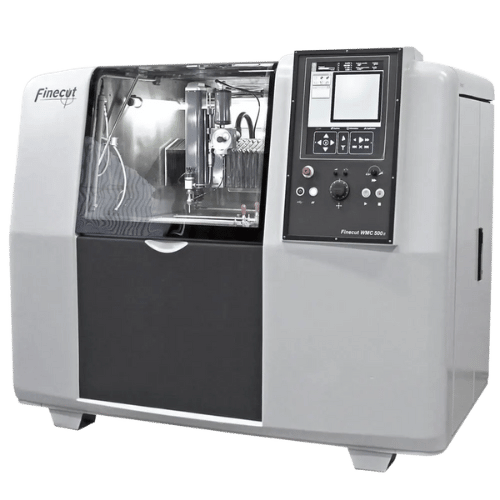
FAQ – Micro Waterjet vs EDM Cutting