Estimated reading time: 21 minutes
Learn About Waterjet:
Waterjet Cutting Technology & How It Works
What you will learn about the waterjet technology:
- Types of waterjet machines
- Benefits of waterjet cutting
- Types of material a waterjet can cut
- Cut quality and precision
- The waterjet control system
If you are looking for an introduction to what a waterjet cutting machine then this article will provide you with the understanding of how waterjet machines works, the different waterjet technologies, and which materials it can cut, in the most economical way.
What Is a Waterjet Cutting Machine?
Waterjet cutting is a technology that is based on the use of one or several jets produced from very high water pressure with high power density. A waterjet cutter can deliver up to 30 kW of power within a fine, high pressure waterjet at the size of a needle, and can cut almost any material. The waterjet can be used either to cut directly (pure water) or to accelerate abrasive particles that erode the material (Abrasive Waterjet).
Types of waterjet cutting technologies
Waterjet technology is utilized in several types of cutting machines, such as budgetary waterjet cutters, traditional pure waterjet and abrasive waterjet cutting machines with varying levels of complexity and precision, and the ultra-precise micro abrasive waterjet machines. While these machines serve different purposes, they all rely on the same material removal process, which involves particle erosion powered by a high-speed waterjet.
What Are The Applications Of Abrasive Waterjet?
Traditional waterjet machines find applications in diverse industrial sectors, ranging from stone industry to Aerospace. Typically, these industrial machines are designed for handling large workpieces on a sizable cutting table. The traditional waterjet machine market can be divided into two segments: a low-cost market with basic machines and a high-end market offering advanced multi-axis machinery capable of meeting the accuracy requirements of aerospace applications within large work areas.
Budgetary waterjet cutters
These waterjets typically operate at lower water pressures and feature cost-effective mechanical designs. These machines are often used in educational institutions and small workshops that don’t require high precision and prefer to handle cutting tasks in-house to reduce lead times.
Traditional waterjet machines
The traditional waterjets find applications in diverse industrial sectors, ranging from stone industry to Aerospace. Typically, these industrial machines are designed for handling large workpieces on a sizable cutting table. The market for traditional waterjet machines can be divided into two segments: (1) low-cost market with basic machines and (2) a high-end market offering advanced multi-axis machinery capable of meeting the accuracy requirements of aerospace applications within large work areas.
The following illustrates the components of a micro abrasive waterjet:
Benefits of Waterjet Cutting Technology
- It is an extremely viable process that can cut practically any material (even at great thicknesses)
- The same tool setup can be used for almost all materials
- No heat effects on the cut surface
- Virtually no mechanical damage to the cut surface
- Narrow cut width of the jet (about 0.5 to 1.2 mm) depending on the size of the focusing tube, which saves material
- Narrow omnidirectional jet can cut complex geometries
- Low cutting forces (< 50 N) means low requirements for clamping and fixturing
- Can cut thin material (with the advantage of low cutting force)
- Cut thick material (300 mm thick steel and titanium are being cut)
- Can cut stacked material (however, gaps between layers should be avoided by clamping)
- Minor or no burr formation
- Easy to use multiple cutting heads for parallel cutting, thus raising productivity
- The need for subsequent machining processes can often be eliminated
From an environmental perspective, an abrasive waterjet cutting machine is attractive because with natural materials, sand and water, it uses nature’s own tool for manufacturing, namely erosion.
Non-Thermal cutting
The abrasive waterjet cutting machine cuts without significantly heating the material; consequently, the hazardous metal gases as well as electromagnetic and ultraviolet radiation formed by some thermal methods can be avoided, which is desirable for work environments. It is, however, important to keep in mind that used abrasive material will contain an addition of erosion fragments from the cut material.
The advantages of non-thermal cutting are especially appealing in the precision engineering industry (including medical device, fine mechanics, optics and electronics, etc.), leading to the development of micro abrasive waterjet machine tools. These ultra-precise machines provide wireless EDM (Electrical Discharge Machining) level precision.
High Water Pressure
High pressure water, at 400 MPa or more, is conveyed in stainless steel tubing to a nozzle, usually of 0.1 – 0.3 mm in diameter. As the water escapes the nozzle, it approaches a velocity of 900 m/s. The jet stream of water leaving the waterjet nozzle is determined by the pressure generating the jet, which is normally in the range of 2 to 3 liters per minute.
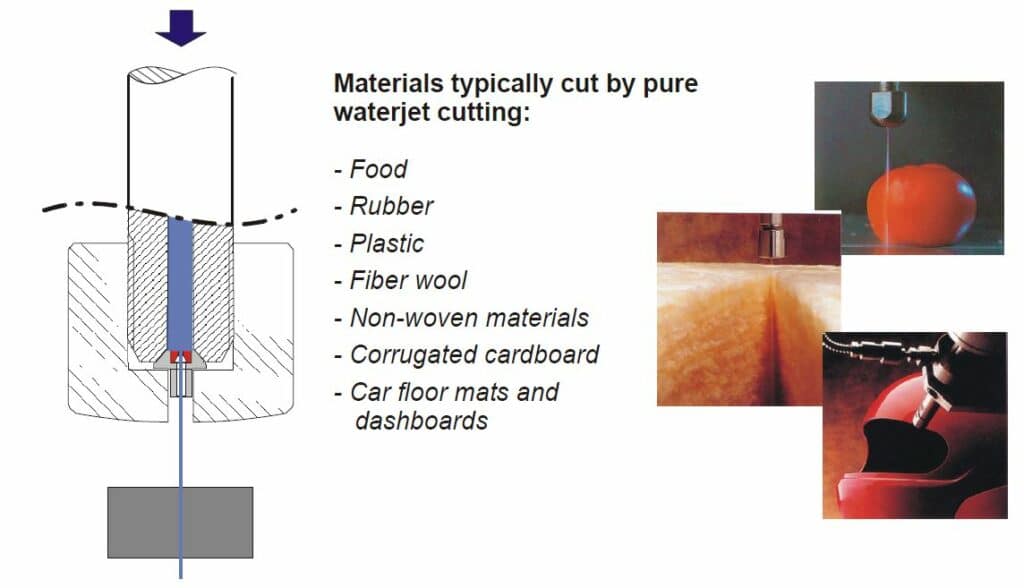
Pure Waterjet Cutting
The water jet cuts soft materials by displacing or eroding material from the workpiece.
Plastics (both solid and foamed), rubber, floor mats and other non-woven materials, plywood and corrugated cardboard are examples of materials which can be cut in this way with a pure water jet.
Even softer metals, such as tin and lead, can be cut this way with the advantage that the material gives way under the pressure of the water jet, while still remaining as a burr on the workpiece; this is especially advantageous in the case of lead which should not be allowed to enter the wastewater system.
Thin and light materials are often cut at high speeds, but even 100 mm thick rubber can be cut, although at lower speeds. This technique of cutting with a stream of water only is known as pure waterjet cutting.
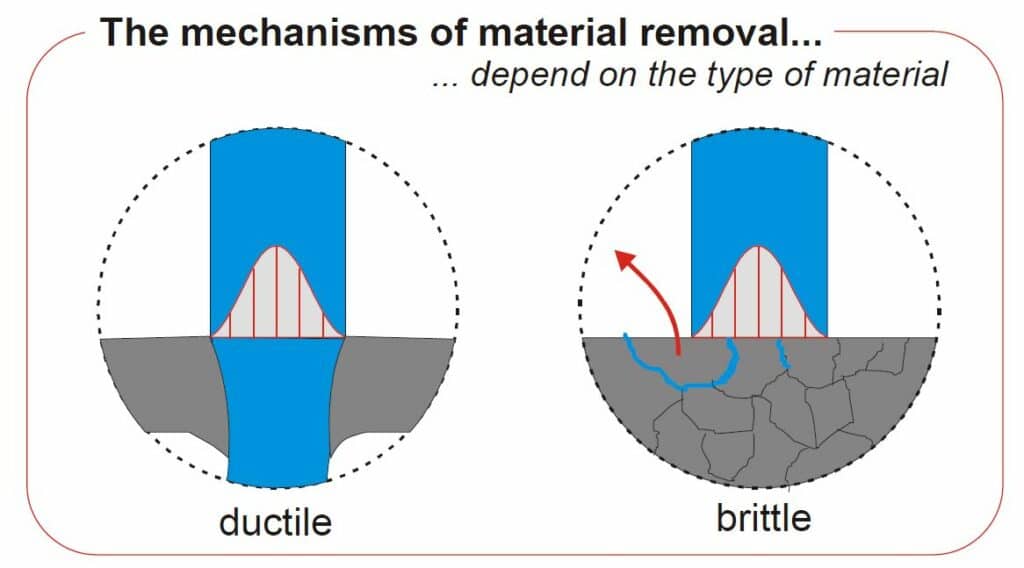
Fibre materials are another group of materials that can be cut to advantage with a pure water jet.
When the stream of high pressure water strikes this type of material, the cracks become pressurized. The pressure causes the cracks to propagate, and a network of cracks causes material to quickly disintegrate and be washed away by the water.
The cutting of glass fiber wool was actually the first Swedish application of waterjet cutting; it was used at the Gullfiber Company in Billesholm as early as 1974. In fact this has received international attention as one of the early industrial applications of waterjet cutting.
The combined capacity of waterjets to cut soft plastics as well as brittle fiber material is especially useful in the cutting of carbon fiber and fiber-reinforced plastics (FRP). In this application the waterjet cutting technique offers important advantages: it gives a fine cut and also eliminates dust generation since the material removed becomes bound to the stream of water. Hence, this feature also reduces a problem in the working environment where these products are machined.
Abrasive Waterjet Cutting
During the 1980s, a breakthrough was made in waterjet technology. By adding abrasive material to the waterjet, a completely new process was generated, which led to an enormous expansion of applications for waterjet cutting.
Practically any material could now be cut, and cutting metal and concrete of dimensions up to 300 mm or more has been reported. The new method, now known as abrasive water jet (AWJ), was quickly developed, since it was based primarily on the same high-pressure components as the pure waterjet cutting with the addition of an AWJ cutting head, by which the abrasives could be added, by means of an abrasive feed system.
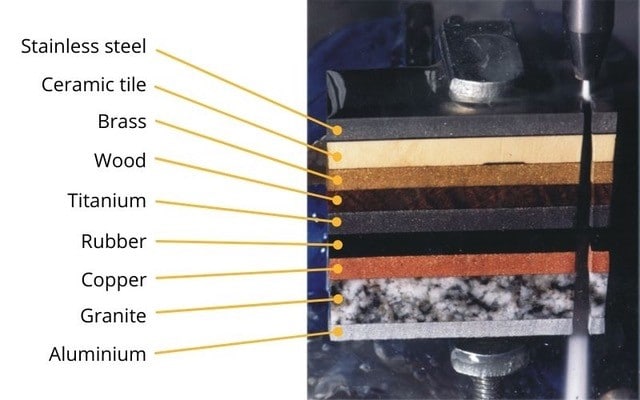
Abrasive Waterjet Cutting Process
Although the capability of the AWJ cutter is capable of cutting virtually all materials, a fundamental understanding of operating parameters can be quite helpful for optimizing the cutting performance as well as the economy of the process. Below the main operating parameters listed in the picture below.
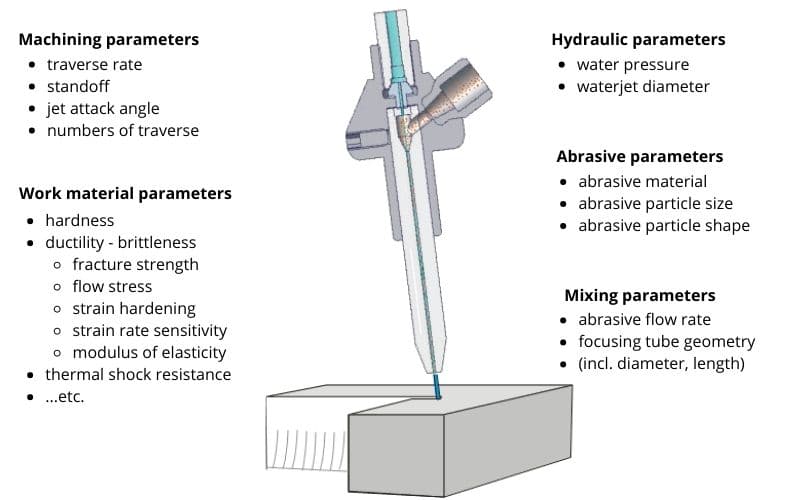
The performance of an abrasive waterjet cutter is controlled by a rather large number of parameters, including the above mentioned main parameters. Cutting capability is ultimately determined by the jet-material interaction resulting from the process parameter selection and the cutting conditions obtained from the machining parameter settings. The cutting results obtained are, for example, cutting speed, depth of cut, kerf width, surface finish or material removal rate.
The Operating Principle of the Abrasive Cutting Head
The main parts of the cutting head are a straight inlet tube that stabilizes the stream of incoming water, a primary nozzle or orifice, a mixing chamber with one or more feeding ports for abrasives, and a mixing tube or focusing tube.
The waterjet formed in the orifice is gradually broken into small drops in the cutting head. In the mixing chamber, these drops transfer energy to the abrasive particles (usually garnet grit) which are fed into the cutting head and accelerated to high speeds.
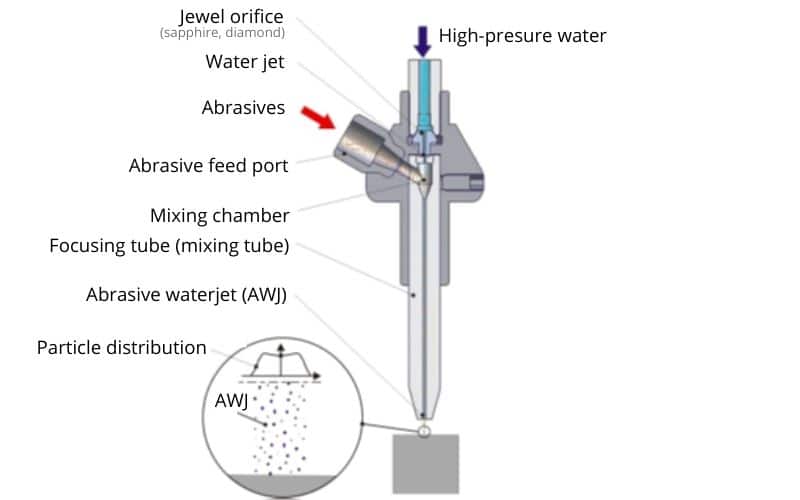
The Mix of Abrasives vs Pure Water
Abrasives and water are then focused into a water jet stream in the mixing tube. The AWJ thereby becomes a stream of particles without any real core of water. By volume the mixture of the water jet stream is about 4 % water, 1 % abrasive and the rest is air.
It is highly critical that both nozzles should be aligned to avoid losing power in the process. The method extends the same equipment as that used for pure waterjet cutting, with the addition of an abrasive feeder and an AWJ cutting head.
As a simplification, this can be compared with a conventional sand blast nozzle assembly. However, water is significantly more effective in momentum transfer than a gaseous medium: the specific weights of water and abrasive are closer.
When the stream of water passes through the cutting head, a partial vacuum is formed (the Venturi effect), which makes it possible to feed the abrasive into the cutting head. The accelerated abrasive is mixed with the drops of water to form a stream of particles without an actual core of water.
The erosive power of an abrasive waterjet makes it considerably more powerful than a pure waterjet. The diameter of the AWJ stream, and thus the width of the cut, is established by the diameter of the focusing tube, which is usually about 0.5 – 1.2 mm, although dimensions as small as 0.2 mm exist. Jet width below 0.5 mm would be considered a Fine Abrasive Waterjet (FAW) and is the most recent development of efficient waterjet machinery.
Multi-axis Cutting
In recent years, cutting tables with five-axis control of cutting heads have been introduced. These machines generally feature the capacity to tilt and sometimes to rotate the cutting head, which means that beveled cuts can be made along contours. This enables new capabilities such as the following:
- Cutting three-dimensionally, which makes it possible to cut holes and contours in forgings, castings and arched or formed sheet stampings
- Contouring and bevelling for preparation of a welding joint performed in one operation
- Compensation for angularity of the kerf wall. (While one kerf wall becomes angular, the angular inaccuracy of the other wall will be doubled, resulting in a scrap side of the cut.)
Challenges of Multiple-Axis Waterjet Cutting
A problem inherent in a multiple-axis waterjet cutter is the increased complexity of the programming, which means more advanced CAM programs are required, and there are higher demands on the software users.
In addition, the more the jet is tilted towards the surface at an attack angle other than 90 degrees, the more important a constant stand-off distance becomes. This problem is accentuated because the true stand-off distance at the center axis of the jet becomes more difficult to measure accurately as the jet leans to one side. Although this type of machine is still somewhat exotic, the advantages it offers are likely to make it more popular in the near future.
More common, however, are the 5-axis waterjet machine systems made for cutting flat plates.
This type of cutting table can be used to cut beveled edges, for example in welding preparation. They can also compensate for the small taper in the cut that is normally produced in the cutting process. This feature is called Taper Angle Control (TAC).
By making a simple cutting test of three different cutting speeds (fine, medium and rough cut) in the target material the operator receives a sample part. Angularities at these three cutting speeds are then measured and inserted as data into the CAM program.
With this input from the operator the CAM software will produce a program for 5-axis control compensating for the natural kerf taper angle.
Micro Abrasive Waterjet Cutting
Micro abrasive waterjet typically employ a scaled-down version of the erosion-based cutting process, with component designs tailored for finer dimensions. A micro waterjet can typically handle tolerances down to +/- 10µm and a positional accuracy of +/-2.5 µm or even better.
The design of micro abrasive waterjets significantly differs from traditional abrasive waterjet machines, and their precision demands the use of high-end components. Therefor, micro abrasive waterjet machines are generally more costly than traditional waterjets, but their enhanced precision cutting and complex cutting capabilities justify the cost. These micro abrasive waterjet cutting machines are available as multi-axis machines, including 3, 4, or 5-axis capability, and sometimes additional axes for achieving precise workpiece access from all necessary angles.
Whereas traditional waterjet machines often use multiple cutting heads, this is not used to a wide extent in micro abrasive waterjet machines as it prevents exact adjustment of the dimensions of each part.
Micro Abrasive Waterjet System Components
- High precision motion system; needs to be well repeating and capable of an accurate tool path movement.
- Cutting table; the area were the work piece is placed
- Waterjet machine tool frame; needs to be stable and rigid for high accuracy cutting
- Waterjet machine fixtures; a stable and flexible fixture is important for the cutting result
- Waterjet CAD/CAM software and operator panel; this is were you load your program and control the waterjet machine
Benefits of Micro Abrasive Waterjet
- Shares the generic benefits of high-pressure waterjet technology, cutting any material without distorting the material properties
- Cut very small radii and narrow slots
- Cuts parts down to +/-10 µm tolerance
- Cut features down to 100 µm width
- Fine abrasives produce fine surface finish down to ca 1 µm in Ra-value
5-axis Manipulation in Micro Abrasive Waterjet Cutting Machines
The traditional way of reducing taper in a three-axis waterjet machine is to reduce the speed. This is effective in most materials, but for very hard materials there will typically be a residual taper that is difficult to remove.
For this a five-axis manipulation can be used, where the nozzle is tilted to compensate for errors.
To achieve a taper-free cut with a three-axis micro abrasive waterjet machine normally requires cutting at speeds nearing 10% of the speed of a separation cut. This means that the surface quality will be fine at significantly higher speeds that are being used to eliminate form errors. Therefore, the concept of tilting the jet while cutting precision parts has a great potential of reducing cutting times. With twice the cutting speed, the added cost of five axis manipulation can often be justified by a quick return of investment.
Abrasive Waterjets (AWJ) vs Micro Abrasive Waterjets (MAW)
Micro abrasive waterjet (MAW) generally refer to jet diameters from 300 µm and smaller. Most operate by principles of a miniaturized traditional AWJ cutting head design. Typically, these cutting heads have a design optimizing precision over cutting speed. Also, other designs are being used to facilitate even finer jets.
The micro abrasive waterjet cutter is up to 10 times more accurate than the traditional waterjet and is suitable for fine mechanical products. The traditional waterjet is less accurate, gives a rougher surface and is used for rough cutting.
The miniaturized cutting system requires premium quality abrasive. Albeit, more expensive the consumption is typically one tenth of what we see in traditional waterjets. A 200µm jet typically consumes ca 0.2 liter water and 10 grams of abrasive per minute. Even though costs of the precision powder are higher compared to traditional waterjet abrasives, the running cost is low.
Complex Cutting of 2-D Geometries
The cutting of two-dimensional geometries in flat sheet and plate materials of any thickness up to 300 mm is the most widespread application of traditional AWJ cutting. However, many companies, for various reasons, advertise the method as suitable up to 100 mm. For the micro abrasive waterjet, the fine jet’s cutting power is lower. Therefore, max thicknesses vary from 10 to 50 mm depending on what jet size is applied.
Two-dimensional AWJ cutting offers several advantages over other cutting methods in:
- It is very quick and easy to set up and program the system for different
- applications, since everything is cut with the same tool;
- Closed contours can be cut, as the AWJ is able to pierce a starting hole;
- Generally, machining can be done to within a tolerance of ± 0.1 mm in materials up to 100 mm thick. For micro abrasive waterjets a tolerance of ± 0.01 mm, or even better, can be achieved depending on material and geometry;
- As the cutting forces are small, clamping requirements are relatively simple;
- The narrow jet diameter facilitates cutting complex geometries in relatively small parts;
- The method produces a cold cut without any significant thermal or mechanical damage.
A Flexible Cutting Method
The capacity of the abrasive waterjet beam to cut virtually all materials offers a very flexible method: the same tool can be used to cut most materials, even without adjustments other than cutting speed.
With modern CAD/CAM software, parts can be machined easily and quickly; the software helps to adapt both the tool paths and traverse rate to the desired quality of cut. This makes the technique suitable also for manufacturing prototypes and smaller series.
The waterjet job shop is able to cut almost any material; this flexibility makes it easy to turn to them for the most diverse cutting needs. If you later wish to produce something in higher volumes on a larger scale, you will naturally need to decide whether waterjet cutting or another method is the most cost effective choice. However, the micro abrasive waterjet is in later years becoming more widely used also for large volume series production, based on its unique benefits.
Faster cutting speed with abrasive waterjet
With a Micro Abrasive Waterjet you can often gain a lot of time if productivity and cost effectiveness by using 5-axis manipulation where you compensate for taper. This can allow cutting with a cutting speed that provides an acceptable surface finish but still has a tapered cut. By compensating taper, a cutting speed up to two or even three times faster has been demonstrated. It is worth checking the return of investment for the added cost of 5-axis manipulation. Often it has earned its cost within a year in increased throughput.
Handling Complex Geometries
Since the small jet diameter makes possible a narrow cut width, this pointed tool offers good conditions for cutting complex shapes, even when the dimensions are relatively small.
Waterjet Cutting Software
A majority of cutting applications are made in two-dimensional paths, which requires a controller that at least interpolates 2 servo axes simultaneously. A simple waterjet cutter may run only two interpolating axes and a manual standoff adjustment for the Z-axis.
Typically, the Waterjet Cutting Software includes a data base that proposes a cutting based on material and thickness of the part to be cut. To enable good cutting results the waterjet cutting software also needs to adjust cutting speed cut in corners and small radii. For this requirement make sure your CAD/CAM software was developed for the waterjet process.
On waterjet cutting machines 3 axis control systems are the base standard. A capable waterjet cutting software can import 3D part models and follow a height contour interpolating three axes simultaneously. To enable cutting with compensation of form errors or to produce more complex 3D geometries, a 5-axis controller is required.
Full 5 axis control normally introduces the concept of programming motion in respect to a tool center point (TCP). This means that the 5-axis controller enables simultaneous synchronized motion of 5 axes that allows moving along a 3D path in the workspace with a possibility to also vary the jet angle towards the TCP while moving along the path.
Smooth Motion Control For High Precision Cutting
To obtain high-precision parts with the micro AWJ cutter, a smooth and precise path motion control is required.
To achieve smooth motion, high-end controllers with very fine interpolation in the nanometer range are used. A closed position feedback loop is used and absolute measuring scales at high resolution are required. These need to be insensitive to thermal influence and in order to achieve this, floating scales of Invar can be used which have virtually no thermal expansion.
When programming micro parts it is important that the CAD/CAM software is adapted to minute parts. The software must handle parts at a resolution that is high enough to meet the precision requirements of the part. Numerical truncation errors may accumulate leading to less accurate parts.
The jet dynamics associated with the material removal processes require the use of CAD/CAM software specialized for the waterjet process. Such software takes into account the physical behavior of the jet as it follows the path along specific geometrical shapes.
In modern CAD-CAM systems it is simple to utilize the 5-axis control system for form error compensation. Parts are programmed as 2D parts and all necessary angular compensation is applied using a compensation database using experimentally assessed data.
What Can a Waterjet Cut?
An abrasive waterjet can cut a variety of materials, including very high-strength material. If a material is to be heat treated (e.g. quenched and/or tempered), it is recommended to carry out the cutting after the heat treatment. (This applies to through hardened material.)
The list below shows some different materials groups and materials that the AWJ process is capable of cutting. If there is specific material you can not find in the table, do not worry, it can in all likelihood be cut.
Laminated & Brittle Materials
Laminated and/or brittle material, such as carbon fiber (CFRP) or engineered ceramics, can be difficult to cut and require a more experienced operator.
Keep in mind that materials which are traditionally difficult to work with need not be so with AWJ cutting. Titanium alloys, for example, are easier to cut than steel.
Composites & Metal Alloys
For AWJ cutting, the composition of an alloy, or possible material inclusions or reinforcements, does not play a major role. Cutting speed in composition materials (alloys) is usually the same as that used in the base material. The hardness of the base material is the most influential factor for each group of materials.
The Waterjet Cut Quality
There are different cut quality classifications for traditional AWJ and micro abrasive waterjet (MAW), where the MAW classification is extended with more quality classes.
Waterjet Cut Quality Classification 1-5
Cut quality is usually divided into five classes ranging from an extra rough quality index, Q1, to an extra fine quality index, Q5.

Cut Quality Classification 1-9
Cut quality classes Q5-Q9 do not have much difference in surface roughness, it is more the conicity in the cut that differs between the different quality classes, where q=9 has totally parallel walls.
The cutting speed for quality class Q9 is only 10% of the cutting speed for Q1. For an economical cutting, you should not choose a higher quality class than needed.
References:
FAQ
The concept of micro abrasive waterjet (MAW) was initially launched by Donald S. Miller in 1998, who demonstrated cutting extremely fine parts with an MAW of 50 µm jet diameter. This technology was industrialized about a decade later by the introduction of commercially available micro abrasive waterjet cutting machine.
The concept of bringing the benefits of high-pressure waterjet technology into fine mechanics/ mechatronics offers important opportunities for advanced fabrication and product development in a wide scope of applications. Today, ultra-precise high pressure waterjet cutting machines is a fast-growing branch of waterjet technology with market awareness of the new capabilities being the main market driver.
An abrasive waterjet can cut virtually all materials such as wood, rubber, glass, metal alloys, ceramics, carbides, nitinol, combined materials etc. It can also cut combined materials with complex structures, e.g. sandwich materials, like carbon fibre reinforced plastics with honeycomb. Harder materials such as alumina or zirconia generally require harder abrasive material to obtain an efficient waterjet cutting process.
Tempered glass cannot be cut with a waterjet as it has a stress balance where any disturbance will make it crack. – Diamond is difficult to cut due to its extreme hardness. Theoretically, it can be cut but it requires an abrasive material in the cutting process that is extremely hard which will give impractically short life length of the focus tubes currently available.
A 3-axis waterjet is a high pressure waterjet machine with a motion controlled cutting head that allows the machine to operate on 3 axis, in X, Y and Z direction. It is used for cutting 2 dimensional parts. Depending on programming it is possible to follow a contour also in Z direction.